SRM damage assessment
Tech data at your fingertips
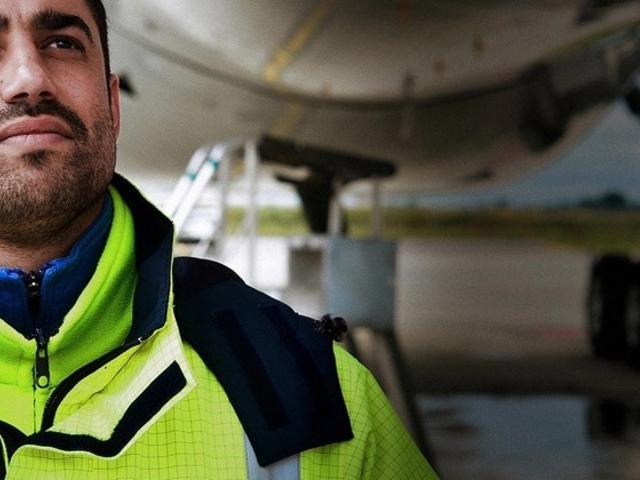
Discovering damage on an aircraft during operations can create stressful situations where the operator’s engineering maintenance teams must assess the damage, potentially manage an AOG*, and still try to dispatch the aircraft without delay.
Damage assessment requires line mechanics to collect and organise data in a structured manner before checking if this damage is within allowable damage limits provided in the Structural Repair Manual (SRM) or if a repair is required.
The process can take time and effort, requiring numerous exchanges between the mechanics at the aircraft and the maintenance engineering team in the office, and may mean a potential delay to the return to-service of the aircraft pending either an authorisation to fly or the need to repair before resuming operations.
Time is critical in such situations but now Airbus customers can use a mobile application to enable digital damage assessments on-site at the aircraft. Let’s discover what SRM for Mechanics (SRM4M) is, and how it can support operations thanks to faster damage assessment.
*AOG: Aircraft On Ground - critical situation that can lead to delay and costs for customers
Let’s follow Mike, a mechanic working in line maintenance:
“As a line mechanic, I frequently need to carry out inspections of the aircraft to identify any signs of damage. This may be because of a lightning strike, or damage sustained during ground operations of maintenance.
Recently, I had to inspect an A320 during a walk-around before a flight. Once at the aircraft, I found damage on the fuselage.
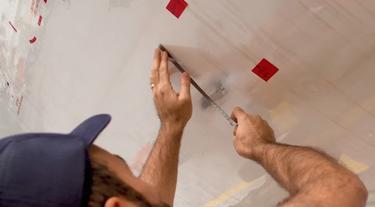
Photo Copyright Airbus
So I opened the SRM for Mechanics app on my tablet and entered all the aircraft details. I could choose to select by MSN or by registration number.
The damage assessment in the app took me through a series of simple questions to select the damaged part and the damage type from among several possibilities.
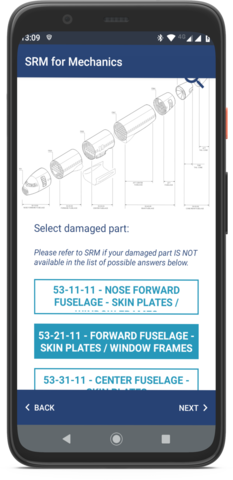

I answered several other questions to clearly define the damage characteristics and location, and to specify information required for the assessment as per the SRM task.
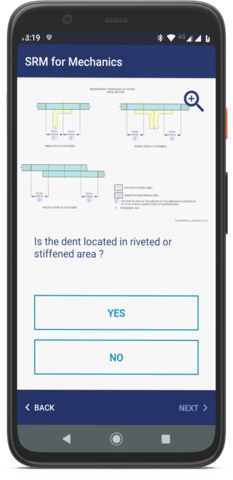
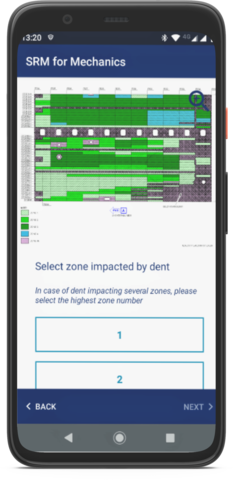
Examples of questions in damage assessment
I was able to go through all steps of the assessment as per the SRM by providing my inputs in a linear process. At the end, I received a clear result based on decision trees embedded in the app.
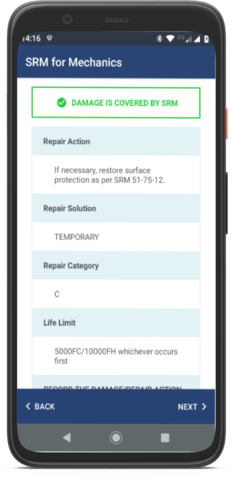
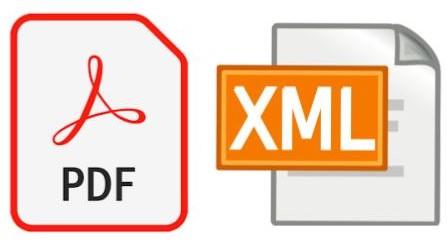
The app automatically generated a full damage report - in pdf xml format - which I immediately sent to the maintenance engineering team along with relevant photos of the damage, to prepare the aircraft dispatch according to the CAMO* duties.
*CAMO Continuing Airworthiness Management Organisation. Organises and manages documents and publications for Maintenance Organizations Part 145 and Part M approved.
This whole process was very fast and easy, and I saved quite some time in performing my tasks of identifying, logging and assessing the damage with the SRM, as well as time spent in exchanging damage data with the maintenance engineering team.
Overall, we could return the aircraft to service much sooner. I was maybe lucky this time that the damage I assessed was covered by the SRM, allowing the aircraft to fly, but even a NO-GO result helps by enabling a faster decision when damage occurs during operations.”
Key features
- Easy-to-navigate app for faster damage assessment, reducing operational interruptions
- Covers many of the typical damage occurring in operations
- Guides the user through damage assessment in real time at the aircraft, based on SRM
- Gives a GO / NO-GO result
- Generates a digital damage report with SRM assessment
- Technical content approved under same EASA delegation as the SRM
- Mobile app available on iOS & Android stores
- Enables user to take photos (new in 2022)
- Enables management of download access rights (new in 2022)
What type of damages does the app cover?
The app includes some of the SRM tasks related to Allowable Damage Limits (ADL) in damage-prone areas on the external surface of the aircraft, covering structural components such as doors, fuselage, wings and stabilizers.
The technical content for the A320ceo should cover many of the typical damages occurring in operations such as dent, lightning strikes or rework. If not, it will take only a few minutes for the mechanic to realize it, so it is still worth trying!
SRM for Mechanics: same content, mobile solution
- Technical content aligned to the SRM content in airnavX
- Publication synchronized with the SRM quarterly revision cycle
Aircraft deployment and dates
Airbus deployed SRM for Mechanics for the A320ceo and A321ceo in 2021, followed by the A319ceo in 2022. The plan is to continue deployment in 2023 for the NEO. This app is also available for MROs.
How to access the app
Airbus customers can download the mobile app from the stores (see below). A link in the app enables them to download a Tech Data Package thanks to a connection to the AirbusWorld customer portal. Once this is done, the app works offline.
For further information, customers can check the Airbus Services store or contact their Customer Service Directors. Airbus SRM for Mechanics Official: App Store or Google Play (Accessible via mobile devices only)
Co-built with customers
The journey of defining a new product started in spring 2019, with a cobuilt phase involving several airlines, including American Airlines, EasyJet, Finnair, GulfAir, Jetstar and TAP. The concept already shaped was improved thanks to customer feedback leading to the new solution deployed.
Join the SRM Working Group
Airbus customers can join the SRM Working Group by contacting its chairman, Dominique CHARLIER (dominique.charlier@airbus.com).
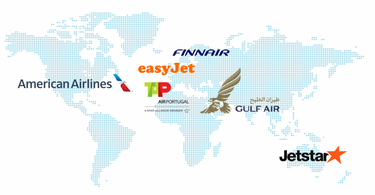
Conclusion
SRM for Mechanics was born to support customers, bringing a digital version of the manual directly to the aircraft, enabling digital damage assessment and higher quality standardized damage reports. Faster damage assessment for faster decision-making is key to reduce grounding time and possible delays to aircraft dispatch - and SRM for Mechanics can be part of it!
This is one of the many improvements already made to the SRM to support customers over the years, along with Flowchart concept, Generic ADL, Weight Variant removal, Technical content enrichment with Dent & Scratch task, to name but a few.
Looking at the bigger picture, SRM for Mechanics integrates with other Airbus services such as Line Family GSE (Ground Support Equipment) for damage characterization and eTech 3D Repair for damage recording.
With SRM for Mechanics, and other technical data products such as GenEWIS, Airbus is paving the way toward digitalization of the technical data ecosystem for availability at the aircraft.
#AirbusServices - e-Store in Airbus World
*News updated on December 2nd
Your media contacts
Contact us
Stéphanie PANISSET
HO SRM
Laurent LIBERGE
Tech Data Customer Offering - Manager - AIRBUS