Cabin Disinfection
Evaluating different technologies
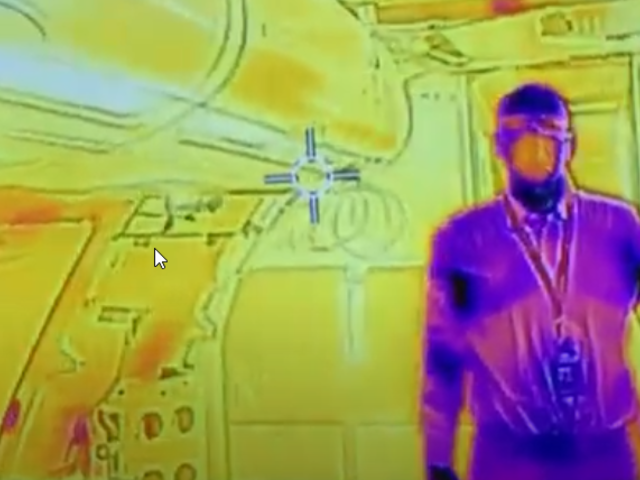
A single aircraft in a single day may see hundreds of people - passengers, crew and ground staff - entering its cabin. Each person will probably touch several surfaces - maybe even several times; from the cabin stowage bin to their seat buckle and arm-rest, from their touchscreen and tray to the bathroom facilities. So how can we reduce the risk of exposure to a virus in aircraft cabins?
Disinfecting cabins using existing or future technologies could mitigate the risk. Airbus has already conducted a series of studies, tests, simulations and analysis of new methods to establish their impact on the aircraft environment and materials.
Why review disinfection?
Several scientific studies have shown that the SARS-CoV-2 virus can remain viable and infectious on surfaces for up to several days depending on the type of surface and the environmental conditions. Consequently, aircraft operators might be required by authorities to increase the frequency of aircraft cleaning.
Airbus has been working with numerous industry partners and regulatory agencies across the aviation network, and has tested different solutions for the aircraft interior - including the cabin, cockpit and crew rest areas - in regards to cleaning and disinfecting. These solutions are in addition to the methods already described in its Aircraft Maintenance Manual (AMM) and the Aircraft Maintenance Publication (AMP) for the A220.
Disinfecting: going beyond cleaning
Cleaning removes visible soil (such as organic and inorganic material) from objects and surfaces and is normally accomplished manually or mechanically using water with detergents or enzymatic products. Thorough cleaning is essential before high-level disinfection and sterilisation because inorganic and organic materials that remain on the surfaces can interfere with the effectiveness of these processes. Cleaning does not kill germs, but by removing them, it lowers their numbers and the risk of spreading infection.
Disinfection eliminates many or all pathogenic microorganisms on inanimate objects. This process does not necessarily clean dirty surfaces or remove germs and viruses, but by inactivating germs and viruses on a surface after cleaning, it further reduces the risk of spreading infection.
Exploring disinfection technologies, their benefits and disadvantages
First of all, testing had to take into consideration a number of factors including the efficacy of the solution, or how well it performed during tests; and its effectiveness, or how well it would actually perform in the real world. The process time to apply the solution would affect resources as well as turnaround time. Aircraft material compatibility needed to be studied in terms of discoloration, flammability, tensile strength and corrosion. And of course, it was key to consider the health and safety of staff handling the solution and of passengers and crew.

On top of what is already described in the Aircraft Maintenance Manual (AMM), and in the Aircraft Maintenance Publication (AMP) for the A220, Airbus investigated several disinfection methods:
- Electrostatic fogging and spraying
- Gaseous hydrogen peroxide treatment
- Ultra Violet (UV-C) light treatment
- Thermal treatment and antimicrobial surfaces
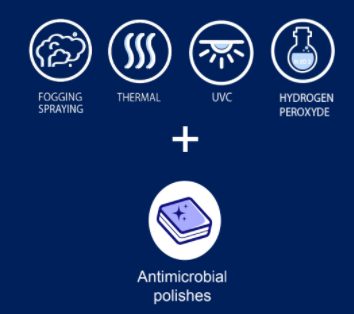
Testing in Cabin Zero
Cabin Zero is an Airbus cabin test centre. The tests below were carried out in a cabin section mockup, within an environment close to that of a real aircraft.
Watch our "A clean cabin for safe flying" video on Youtube
Electrostatic fogging and spraying
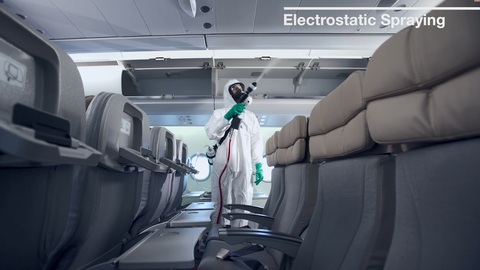
These treatments are based on the generation of liquid droplets which will widely disperse the disinfecting liquid into the cabin. The main advantage of fogging and electrostatic spraying is that it enables large areas to be treated, in a short time frame. However, Airbus identified risks of accumulation of disinfecting agents that could be induced by the usage of these methods, as well as a potential effect on cabin material in the mid or long term.
How it works
- Fogging is the indirect application of a disinfectant liquid as a mist or fog to an area. The purpose is to create and disperse a disinfectant aerosol to reduce airborne microorganisms and also to apply disinfectant to surfaces that may be difficult to reach. The term “fogging” means that generally small-size particulate matter (not gaseous) is suspended in the air.
- The disinfectant is sprayed through a fogging machine which aerosolizes the liquid so that it is uniformly suspended in the air and can coat all surfaces in the cabin. Fogging is achieved using either a static, purpose-built system with strategically placed nozzles or, more commonly, a mobile unit.
- Electrostatic spraying systems deliver charged droplets which are actively attracted to surfaces, including the back sides and crevices of surfaces, regardless of the direction of spray for complete wrap-around disinfection coverage.
- Electrostatic spraying may enable a more targeted application using less disinfectant while producing fine particles with controlled shapes/sizes.
Electrostatic fogging and spraying can be done with handheld units, independently from on-ground equipment.
What benefits can be expected?
This quick method of disinfection and its effectiveness is known from other industries. The main interest of chemical fogging is to treat visible surfaces which may be touched by cabin and cockpit occupants, but also to treat non-visible surfaces as the very small particles containing the disinfecting agent are less influenced by gravity, stay in the air, and follow the airflow. Fogging with a smaller droplet size could enable less liquid to be used.
What about potential drawbacks and risks?
- Material compatibility: disinfecting agents may adsorb* on, or be absorbed by the cabin and aircraft. (*Adsorb: cause a substance, usually a gas, to form a very thin layer on the surface of another substance)
- Possible negative effects in the short term (such as a change of surface appearance or haptics) - or in the long term, mainly due to the accumulation of residual agents over time (such as corrosion, reduction of flame retardancy for soft materials).
- Flammability: Fogging or spraying may create a flammable atmosphere when being used with inappropriate agents such as alcohol-based or other potentially flammable liquids.
- On-ground staff need to wear appropriate protective equipment during the application process.
- Spraying on a surface in an uncontrolled manner can result in health risks for humans (eyes, respiratory system, skin irritation, etc.). Moreover, the disinfectant may accumulate over time on surfaces and in materials, and hence may lead to undesired health effects.
- Electrostatic fogging and spraying might damage electronic devices.
Airbus’ assessment
Fogging or large-area spraying may allow disinfectants to accumulate in non-visible aircraft areas. Mid and long-term effects regarding material compatibility in general and corrosion in particular, cannot be excluded when using these methods. Tests on soft materials have shown that the flame retardancy can be reduced depending on the chemical. These methods and associated potential effects would have to be closely assessed and monitored by the operator.
Treatment with gaseous hydrogen peroxide
Hydrogen peroxide (H₂O₂) is commonly used as a strong bleaching agent and as a disinfecting agent (for example in medicine, waste water and in the food industry) and is highly efficient against bacteria and viruses.
Note that here we only refer to the gaseous form.
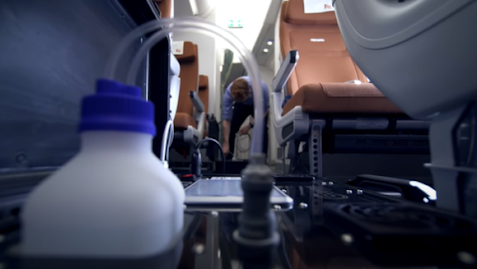
Description
- The hydrogen peroxide (H₂O₂) treatment is known as an oxidising agent and can lead to corrosion if a high humidity environment is created – only gas phase application is considered viable (low humidity). In a pure form it is a pale blue liquid, which can be diluted with water.
- One method for air and surface disinfection is using hydrogen peroxide in gaseous form instead of directly applying aqueous solutions or spraying aerosols.
- Three methods are commonly known to achieve the desired droplet-free generation of hydrogen peroxide gas:
- An airflow at ambient temperature is continuously blown over a high surface material that has soaked up a preheated aqueous solution of hydrogen peroxide.
- An airflow is dehumidified, then preheated above 100 °C; subsequently an aqueous solution of hydrogen peroxide is injected which causes a flash evaporation.
- Photocatalytic generation of hydrogen peroxide from natural humidity and oxygen already in the air is applied at ambient temperature.
What benefits can be expected?
- The effectiveness of a disinfectant such as hydrogen peroxide is proportional to the disinfectant concentration in the air multiplied by the exposure time (at a given temperature and humidity level). In other words, it depends on the concentration of H₂O₂ reaching the surface and the dwell time.
- According to a report from the FAA, 99% of viruses can be inactivated on surfaces when using hydrogen peroxide at a concentration of 10 ppm (parts per million) during an exposure time of 2.5 minutes.
- Potentially, H₂O₂ can be applied at very low concentration (<1ppm) even with the occupants in the cabin. The application time could therefore be longer without impact on turnaround.
- It is an automated process via ground equipment or portable equipment distributed in the cabin.
- The gaseous form enables very homogeneous disinfection within the cabin.
- H₂O₂ disinfects against any kind of microbe (virus or bacteria).
What about potential drawbacks and risks?
- Effective hydrogen peroxide concentration levels and exposure times against SARS-CoV-2 virus are subject to ongoing studies.
- Risk of condensation on cold surfaces leading to subsequent corrosion.
- Damage to materials (e.g. wool, leather, nylon, natural rubber, polysulfide sealants, etc.) when exposed to hydrogen peroxide at too high concentrations and/or exposure duration.
- Potential effects on human health (skin and respiratory system).
- Operators must wear protective equipment.
- A release concentration of <0.5 ppm is required before people can enter an environment after hydrogen peroxide treatment.
Airbus’ assessment
There are potential risks of mid and long-term effects regarding material compatibility and for corrosion in particular. Turn Around Time (TAT) could be impacted by the waiting period required before people can enter the aircraft after the treatment process.
UltraViolet UVC Germicidal Irradiation
UltraViolet Germicidal Irradiation (UVGI) uses short-wave ultraviolet (UV-C) energy to inactivate viral, bacterial, and fungal organisms. The effectiveness of this treatment depends on several variables including the applied UV wavelength, radiation intensity, the dwell time on a given surface, the nature of the germs to inhibit and the complexity of the surface geometry.
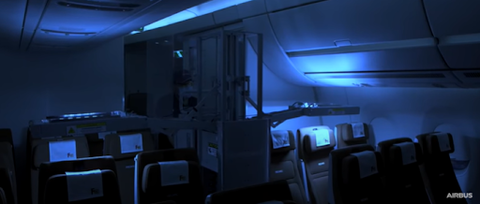
Description
- UVGI uses UV-C energy to inactivate viral, bacterial, and fungal organisms so they are unable to replicate and potentially cause disease.
- UV-C energy disrupts the nucleic acids (DNA / RNA) in a wide range of microorganisms, rendering them harmless.
- Early scientific studies established that the most effective UV wavelength range for inactivation of microorganisms is between 220 and 280 nm, with peak effectiveness near 265 nm.
- The standard source of UV-C in commercial systems is low-pressure mercury vapor lamps, which emit mainly near-optimal 253.7 nm UV-C.
- Disinfection could be reached by radiating the required UV-C on a given surface for a sufficient amount of time.
- Products advertised on the market use tubular UV-C radiating lamps radiating at 254 nm installed either on a specific trolley that is moved manually along the aircraft aisle or with handheld devices (UV-C wands).
- The required duration of exposure depends on the lamp performance, the distance and orientation to the surfaces to be treated, and the nature of germs to eradicate.
What benefits can be expected?
This quick method of disinfection and its effectiveness is known from other industries. It is semi- automated and could be a faster disinfection process with no residuals or consumables. It is highly efficient as an antiviral. No flammability impact has been noted.
What about potential drawbacks and risks?
- There is a risk that some surfaces, like the angled lower side of the window armrest, receive less UV-C dose while the upper part of the seat headrest receives a higher dose with a risk of quick deterioration.
- For efficient disinfection, movable parts of the cabin need an exposure to UV-C on both sides (e.g. tray table, arm rests, overhead bin covers, lavatory doors, etc.).
- Although UV-C is known to not intrude beyond the dead skin layer, care is required as generally the high energy content of the radiation can have side effects on humans depending on radiated power, duration, and the body part which is being illuminated. Personal protection means must be considered to avoid any skin or eye irritation.
- UV-C lamps contain mercury and therefore equipment must be designed to prevent any breakage of the lamps.
- Though UV light has no effect on metals and ceramics, it affects the molecular bonds of polymers, leads to molecule chain scission and to the creation of radicals that may change the polymer properties (e.g. discoloring, disintegration, tensile strength).
Airbus’ assessment
There are potential mid and long-term effects regarding material compatibility (e.g. discoloration, reduction in tensile strength). The broad effectiveness of this method in the cabin environment is questionable due to several reasons, including the shadowing effect and required radiation intensity.
Thermal treatment
Thermal disinfection is a method using temperatures higher than usual ambient temperature. The effectiveness of the treatment lies in three variables: temperature (T), dwell time and relative humidity (RH).
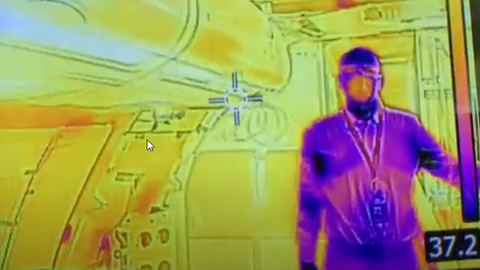
Description
As stated in the World Health Organisation (WHO) guidance on cleaning and disinfection of environmental surfaces, the COVID-19 virus survives in ambient temperatures but is susceptible to heat and standard disinfection methods. Thermal disinfection benefits from the sensitivity of viruses to temperature which, when combined with humidity, can render the virus ineffective.
What benefits can be expected?
- Thermal disinfection in an aircraft environment (cabin, cockpit, crew rest areas) is an automated process which can be achieved by various means:
- Using airport ground support equipment such as Pre-Conditioned Air (PCA) to inject hot air in the aircraft through the low pressure ground connector or directly through the aircraft door.
- Using the aircraft Environment Control System (ECS) or so-called “air conditioning” system.
- Using remote electrical heaters positioned inside the cabin & cockpit and crew rest areas.
- Or a combination of the aforementioned.
- Equipment installed in the cockpit, crew rest areas and cabin of all Airbus aircraft (except the A220) are qualified for temperatures up to 55°C/131°F when powered.
- With heat as the solely effective measure to inhibit viruses, no additional chemicals would be required.
- Ground equipment to perform the disinfection is commonly available around the world.
What about potential drawbacks and risks?
- Potential risk of ageing effects on materials, due to repetitive warming.
- Time required to perform this procedure is not compatible with turnaround time.
- Logistics and preparations required to set up the procedure.
- Potential impact on aircraft operational availability and on turnaround time.
- At least 20% relative humidity is needed, which complexifies the whole process.
Airbus’ assessment
Airbus has conducted tests on its single aisle and widebody aircraft to demonstrate the practicality of any thermal disinfection method (e.g. temperature, duration). This was done in cooperation with medical institutes to evaluate the combination of variables which would allow virus inhibition through this method. Current results have not yet reached a satisfactory conclusion.
Disinfectants
Disinfectants are approved for use on Airbus aircraft if they have no damaging effects on the aircraft in terms of aircraft structure (i.e. corrosion), electronics and avionics (i.e. insulation of cables), sensors (i.e. smoke detection) or the interiors (i.e. installations, seat covers, curtains, monitors, media devices, windows, galleys, countertops, restrooms, etc.).
Due to the delicate nature of instruments, screens and components installed onboard the aircraft, only approved procedures and products must be used in accordance with Airbus guidance (AMM 12-21-12 and AMP 51-26 and AMP 51-31 for A220).*
On the contrary, some disinfecting substances must not be used on aircraft, such as biocidal substances for general disinfection. Operators should refer to the latest AMM (AMP for the A220).
*AMM: Aircraft Maintenance Manual - *AMP: Aircraft Maintenance Procedure
Cabin disinfection involves aviation partners and regulatory bodies throughout the industry, including the aircraft manufacturer, suppliers, authorities, and of course the operators and ground support teams.
In a collective effort to give a clear picture of possible options, Airbus has worked with other industry partners to test several different solutions for efficiency and feasibility.
Electrostatic spraying or fogging, Ultraviolet (UV) light, gaseous H₂O₂, thermal treatment, and antimicrobial polishes: these are some of the solutions which could be used in the future, independently or combined.
Each method presents benefits and drawbacks. Airbus continues to work actively with partners on alternatives which also include antimicrobial coatings, polishes and touchless features. In the meantime, Airbus recommends all operators to continue using the disinfection method referred to in the AMM and the AMP.