Keeping in shape
A350 structure repairs and kits
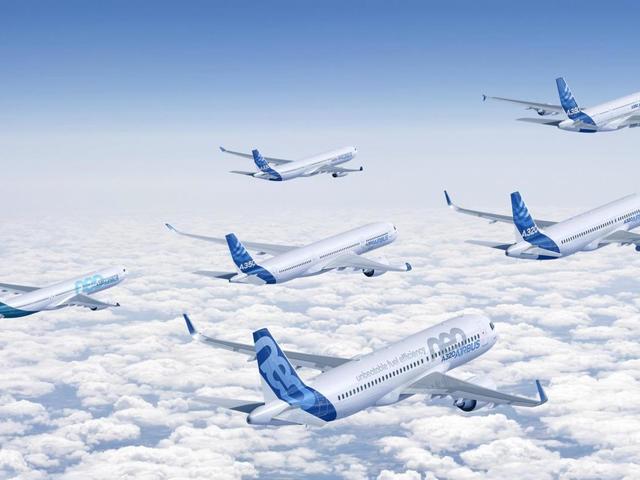
Maintenance and structure repairs are part of the normal upkeep of an aircraft. And this goes of course for the A350, with some slightly different methods due to composite primary structures. Today’s aircraft have been designed using the accumulated, past experience from previous passenger and cargo planes, enabling potential repairs to be identified and planned for in advance.
The choice of repair method will depend on the type of damage, level of severity and the material being repaired - be it aluminium, titanium or carbon. In some cases, solutions can be temporary, taking into account customer needs and constraints.
Designed to be maintainable and robust
Designing the A350 structure meant taking into account different criteria:
- Maintainability:
For customers, this was key to ensure maximum operability of the aircraft and minimum maintenance costs.
- Robustness:
This can be defined as the ability of the structure to sustain in-service loads with no or minimum maintenance action. Changing from a metallic fuselage to a composite one required Airbus to consider all threats (lightning strikes, mechanical impact, scratches) and to define the associated damage. Airbus conducted a survey of in-service damage on single-aisle and long-range programs to define all “prone to damage” areas. Typical damage can be caused by lightning strikes and hailstones. ‘Abnormal events’ damage can occur on the ground from catering trucks, cargo-loading equipment and elevators or during maintenance. Airbus defined airframe zones based on a probabilistic approach between damage occurrence and mechanical impact energy threshold. Basically, the more prone to damage an area is, the more resistant the structure is in order to reduce maintenance operations and repairs. The right balance had to be achieved between the structural weight and the impact resistance.
Detecting and assessing damage
In case of visible mechanical impact damage during operations, ultrasonic Non Destructive Testing (NDT) detection is required. (Non-visible damage is covered by design and does not compromise the structure integrity.)
Customers can perform the detection and assessment without an NDT-qualified inspector thanks to the Line Tool and Line Sizing tool to determine the extent and severity of damage.

Picking the right repair type for the job
Repairs can be divided into three main types: non-structural or cosmetic repairs; standard structural repairs, and major structural repairs. Depending on the damage analysis, temporary and permanent options may be available for both the non-structural and standard structural repairs.
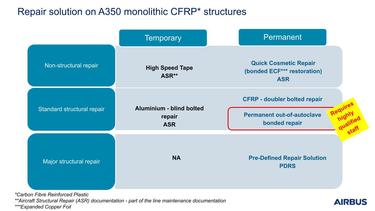
1. Non-structural repairs
Non-structural damage does not affect the structural strength.
A temporary fix can be done using high-speed tape:
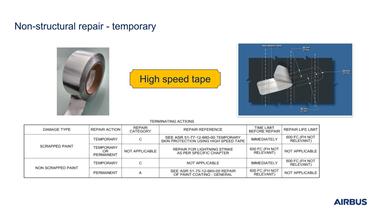
A permanent fix is the quick cosmetic repair:
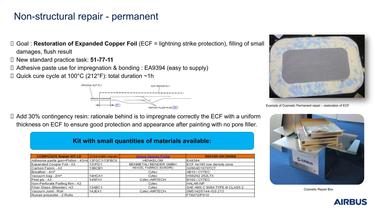
2. Standard structural repairs
There are several options available for composite which will depend on damage location and operational constraints. So there could be a temporary option with life limitation, or a permanent repair (external or flush; bonded or bolted or mixed).
The temporary option is to do an aluminium blind bolted repair:
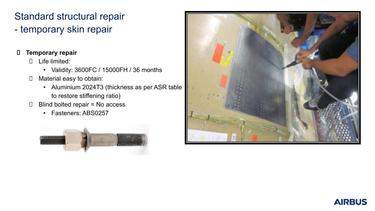
Permanent repairs are done by bolting or bonding or mixed repair types:
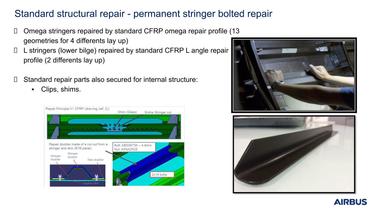
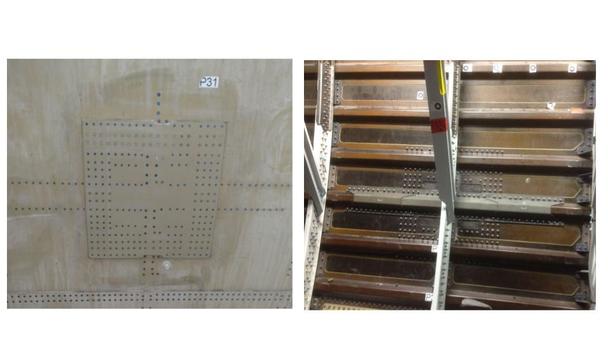
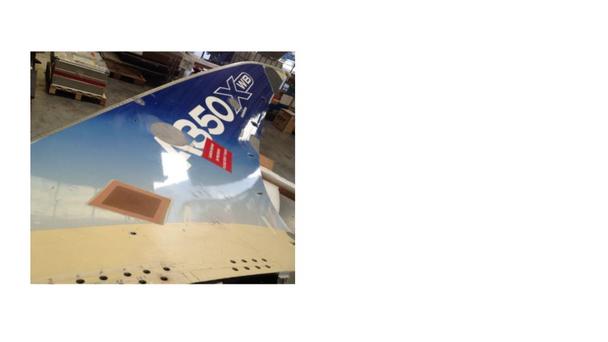
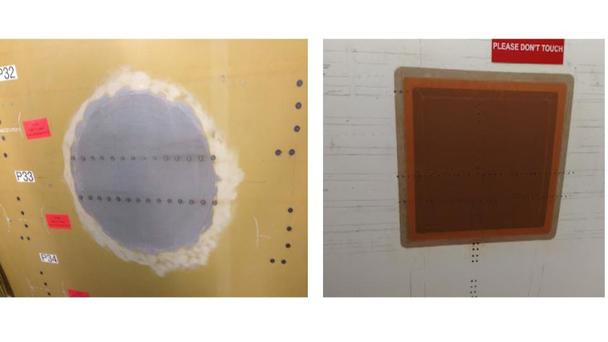
These repairs require specific composite drilling and bonding competences. They can only be carried out by qualified staff who have followed appropriate training.
Refer to Airbus Structure Training catalogue
More details on bolted and bonded repairs in FAST 61.
3. Major structural repairs
These repairs are used where there is significant damage which requires a permanent solution. As the work can be time-consuming and costly, Airbus has developed Pre-defined Repair Solutions(PDRS) to help speed up the repair process.
Pre-defined Repair Solutions (PDRS)
The solutions are ready-to-dispatch kits, which include repair instructions, access and close-up data, parts, hardware, specific tools and Ground Support Equipment (GSE) if required, and embodiment instructions validated in most cases through trials. They have been developed to anticipate typical recurrent repair needs, based on repair analysis from passenger and cargo aircraft, enabling customers to plan ahead.
Typical key risk areas include the cargo loader area, door surroundings, and panels in the hold. Other damage may be inflicted by bird or tail strikes, nose landing gear collapse, tail jack incidents or truck damage.
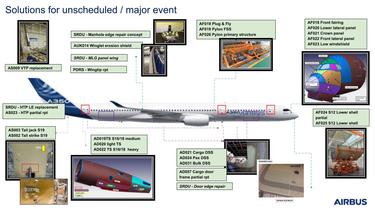
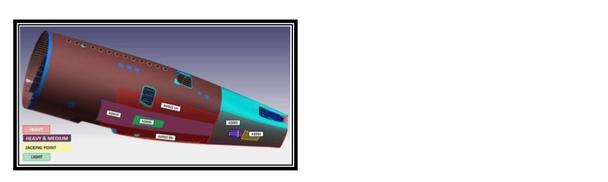
Composite or Carbon Fibre Reinforced Plastic (CFRP) has progressively replaced aluminium in aircraft design over the past years. It helps improve aircraft performance thanks to its lighter weight. It also assists in maintenance and repairs thanks to its increased robustness.
Based on decades of experience in cargo and passenger aircraft with both metallic and composite materials, Airbus has been able to identify areas susceptible to damage during operations and anticipate different structure repair types. This eases the task for operators, helping them to release aircraft back into service as quickly as possible thanks to rapid assessment and temporary or permanent solutions. In the case of major events, the PDRS catalogue provides ready-to-go solutions to gain time and efficiency for airlines, MROs or Airbus working parties carrying out the repairs.
Authors:
Sébastien HANSER - sebastien.hanser@airbus.com
Guillaume FERRER - guillaume.ferrer@airbus.com
Sébastien DUPOUY - sebastien.s.dupouy@airbus.com
Embodiment Industrial Managers, Airbus
------------------------------------------------
Copyright photos and illustrations: Airbus; Master Films: JB Accariez, A. Doumenjou
------------------------------------------------
To view other FAST articles, download the FAST app (available in the App Store and Google Play)