A321XLR approaching the finish-line for Certification and service entry…

As the A321XLR’s five-year long flight test and EASA certification programme draws to a close and the first series production aircraft are handed over to the commercial teams for delivery to launch customers, we look behind these scenes at what has led up to this, and the main milestones achieved this year.
Over the years Airbus has applied numerous major upgrades and modifications to all its airliner products, in the spirit of continuous incremental innovation to enhance their capability and value for airlines. The most well-known of these evolutions have typically included new ‘weight variants’ for range and payload increases, aerodynamic enhancements (such as wingtip sharklets), flight control tweaks, new door configurations and cabin flexibility options, higher engine thrust options, cockpit avionics evolutions and navigation capabilities and so on.
While such design changes to an aircraft ‘Type’ all need to be certified by the airworthiness authorities (eg. EASA and FAA), the associated development campaigns by the aircraft manufacturer are typically low key in terms of testing and demonstration – culminating as an amendment in the respective Type Certificate Data Sheet’s next revision without any fanfare.
However, every so often Airbus introduces a major new airliner derivative programme which grabs the attention of the industry – bringing game-changing capabilities that go beyond the scale and scope of the usual enhancements throughout a commercial aircraft’s life-cycle.
Unprecedented capabilities to test and certify
Very soon, the A321XLR will bring airlines the flexibility in a single-aisle aircraft for both point-to-point operations of up to 4,700nm as well as high-density shorter-range routes, offering a standard mix of premium, premium-economy and economy classes – while consuming 30 percent less fuel than its predecessor.
For this new member of the A320 Family, the engineering design changes go deep into the aircraft’s structural architecture and systems – affecting practically every ATA chapter. Examples include the A321XLR’s new single-slotted inboard flaps, upgraded flight control system, uprated landing gears wheels and brakes, a new fuel system, new water and waste system, plus an enhanced cabin heating system for long range operations.
Most significantly of all, the aircraft features an entirely new centre fuselage incorporating a conformal 12,900 litre ‘rear centre tank’ (RCT), a dedicated new fuel system, new fibre-metal laminate materials with fire-retardant properties on its lower shell, and a new larger and reinforced belly-fairing. The latter – in combination the RCT structural design – allows the aircraft to sustain emergency belly landing conditions. Moreover, being equipped with sliding pads, the extended fairing also acts as a cushion for the aircraft to slide until it comes safely to a standstill.
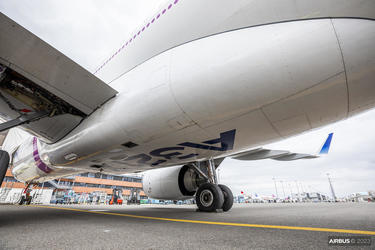
Full-scale certification and development campaign needed
Given all of these major changes which differentiate it significantly from the basic A321neo, it was clear from the outset that the -XLR’s development and certification programme could not simply be achieved in a few months with isolated ‘mod’ testing relying solely on the existing A321neo test aircraft at St Martin’s M81 flight test centre. Rather, a full-scale flight test programme was required with several new dedicated A321XLR representative prototypes, and to be similar in terms of scale and complexity to certifying a completely new aircraft type. Overall this would directly involve around 2,500 Airbus staff in its A321XLR development team.
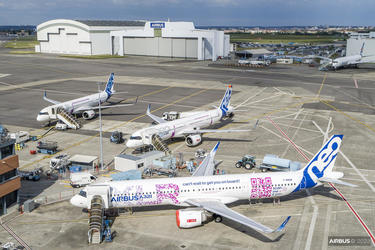
For the -XLR, three dedicated prototype aircraft, incorporating all the new features, were designed and built from scratch. These aircraft would undergo a two-year period of certification flight tests, ground tests, and airline demonstration campaigns – with both CFM and Pratt & Whitney engine types. This would include trans-oceanic route-proving flights in collaboration with launch operator airlines, airports, air traffic control (ATC), and with both Europe’s EASA and the US FAA airworthiness authorities.
While the first A321XLR prototype flew in June 2022, the development journey actually started a few years earlier in 2018 – marked by the definition phase (known as ‘MG3’). This is when the programme's overall objectives and assumptions and the basic architecture were defined, and the initial team that would drive development in the concept phase was established.
From the kick-off meeting with EASA in 2019…
Soon afterwards, in 2019, Airbus’ programme committee formally applied to EASA and convened a familiarisation meeting – which effectively marked the certification kick-off with the authorities.
By 2020, and despite the unfortunate onset of the Covid pandemic, the design phase (MG5-MG7) was well underway, leading to the release of the approved drawings for manufacture of the major component assemblies (MCAs) and delivery to the FAL in Hamburg. By the end of 2021, the final assembly phase (MG9) was underway for the first of the three prototypes that would soon perform the extensive flight test campaign.
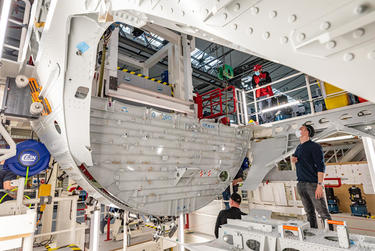
… to wrapping up flight testing and certification in 2024
Fast forward to 2024. This year has been a very busy time for all the teams to implement and finalise all the open points and ‘Special Conditions’ identified together with the EASA and the FAA regulators. As part of this, Airbus worked extensively together with the regulators to ensure the highest safety related to the aircraft’s new RCT design and its surrounding structures, in all operational scenarios.
By the summer, the flight test teams also had brought all the activities to completion for certification of the CFM-powered variant – which will be the first to enter service with Iberia later this year. To this end, both MSN11000 and MSN11058 have flown in parallel: Most recently MSN11000 in 2024 successfully completed the CAT III autoland system tests in a variety of crosswind, tailwind and headwind conditions. The autoland function also needed to be tested with various weight and centre-of-gravity (C-of-G) states – made possible thanks to the transferrable water ballast system which was fitted in this test aircraft. MSN11000 then went to complete the remaining flight tests with the CFM engines.
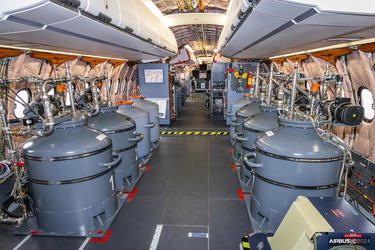
Meanwhile, MSN11058, powered by P&W engines, this year performed testing of the RCT and its fuel system functionality. (These particular tests did not depend on the specific engine type). This marked the completion of all the main tests for the certification of the CFM-powered variant, which was followed by submission of all the documents to EASA.
On completion of its CFM-related flight testing, MSN11058 began its next phase of duties – this time fitted with Pratt & Whitney engines so that the aircraft could perform take-off performance and the exterior noise and tests close to Seville, Spain with that engine type – with a team of around 60 people. MSN11058 subsequently went on to conduct the remainder of the P&W type certification flight tests, to include the CAT III Autoland.
It should be noted that the other member of the three-strong test aircraft fleet was MSN11080. This CFM-powered aircraft was fitted with a full cabin and was used extensively in 2023 for the international route-proving missions with passengers, including launch customer airline participation. It also made a four-day visit to Iqaluit in Northern Canada for cold weather ground testing of the cabin.
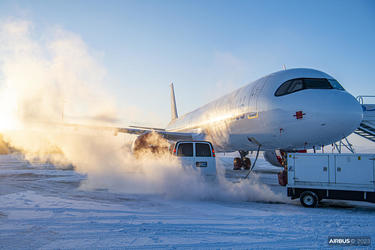
MG13 reached – ‘readiness for service entry’
To date, the three dedicated test aircraft have performed a total of around 1,450 flight test hours in more than 510 flights, as well as ground tests, resulting in more than 700 individual documents which have been submitted to EASA for the certification dossier of the CFM variant. In addition to these, around 4,500 technical airline documents (which include the *ICAs) have been produced for the first customers to be ready for their EIS. At the time of writing in July 2024, with the programme teams having achieved the ‘readiness for service entry’ maturity gate – referred to as ‘MG13’ – the Type Certification for the CFM-powered A321XLR is imminent. This will be followed in due course by the P&W variant.
*ICAs = ‘Instructions for Continued Airworthiness’
Latest news
Continue Reading
A suite of comprehensive services to keep the A220 flying
Web Story
Aircraft
Like all Airbus aircraft, the A220 benefits from innovative services that facilitate its seamless integration into any operator’s fleet.A350F: what makes the world's largest main-deck cargo door a special one...
Web Story
Aircraft
Airbus confirms Hughes as an additional provider of LEO and GEO services for HBCplus
Web Story
Services
Airbus and Panasonic Avionics to co-develop the future Connected Aircraft platform
Web Story
Services
Airbus and Amazon’s Kuiper team-up to offer LEO satellite network for HBCplus
Web Story
Services