Reinforcing cabin hygiene
Antimicrobial solutions
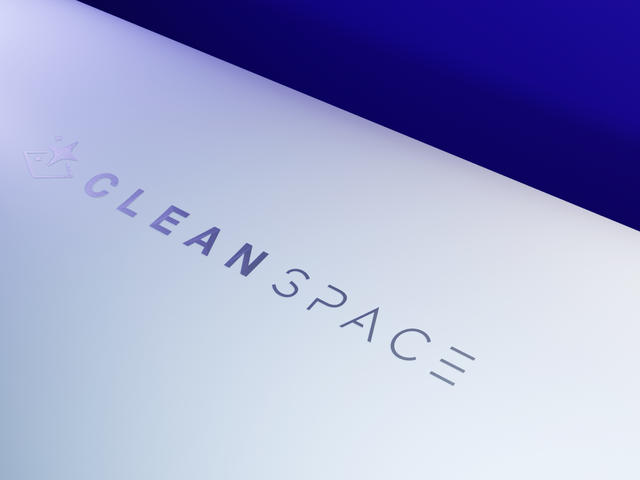
For over 50 years, Airbus has taken great care to design a safe environment for passengers and crew - a priority which remains unchanged for us in today’s world.
Since the onset of COVID-19, passenger concerns about cabin hygiene have increased drastically. Some key existing features of Airbus aircraft interiors that were previously less important for passengers - such as HEPA air filters and touchless surfaces - have now become well-known.
For airlines, getting back to service after being grounded by the pandemic means ensuring the aircraft is a clean and safe environment for passengers and crew. After in-depth studies on different technologies for cabin disinfection, Airbus assessed possible solutions and their advantages and constraints. One solution was to use antimicrobial polishes and a first product is already available for airlines, approved by Airbus for use in its aircraft. Further antimicrobial surfaces and textiles are also under examination and will be coming soon.
Following customer feedback, Airbus is working on different solutions but also on a comprehensive approach to on-board hygiene using “Clean Space” labelling in the cabin. This comprises three key elements:
- Clean Air: Highest air quality for passengers & crew
- Clean Interior: Disinfection methods
- Clean Touch: Touchless functionality and antimicrobial surfaces
Here we focus on the antimicrobial surface solutions that teams are developing and improving.
6 questions from airlines about antimicrobial solutions
Airlines were clear about what they needed in terms of a cabin hygiene solution:
- an easy-to-manage solution which would not severely impact turnaround times
- a cost-friendly solution
- a solution which would make passengers feel more protected in the cabin
- a solution without health side-effects on passengers and crew
On top of these criteria, it was important to consider the amount of potential waste generated (products, cleaning cloths...) from an environmental view.
1. What are antimicrobial technologies?
Antimicrobial technologies further enhance hygiene in the cabin by introducing protection against bacteria, viruses and fungi to surfaces, both in linefit and retrofit.
- Surface polishes and fabric treatments are typically for retrofit needs and have to be reapplied on a yearly basis to keep their efficacy.
- Coatings and textiles have an antimicrobial additive embedded into the material or surface. Their efficacy can last for the lifetime of the part they are protecting and are suitable for linefit as well as refurbishment.
These technologies will enhance the cabin hygiene, as they work 24/7 to self-sanitise the protected surfaces.
Statistical simulation
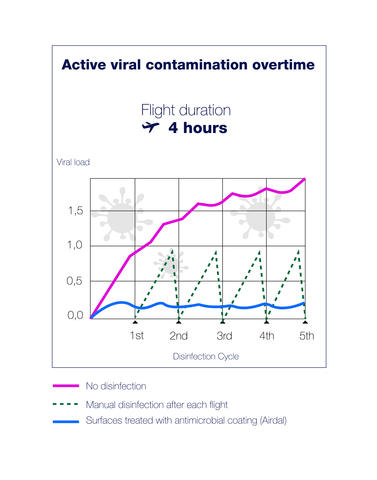
2. Where and how can they be applied?
Airline and passenger surveys conducted by Airbus (based on feedback from 85 customers worldwide) and IATA* have shown that the main hygiene concerns for passengers are the lavatories and frequently touched cabin surfaces. Hence we focused on solutions for both hard as well as soft surfaces. Polishes and fabric treatments can be applied through an easy “spray and wipe” process and require only a few hours of drying time. The whole procedure can be accomplished during a night shift, with the treatment lasting for up to a year before re-application is required.
The antimicrobial linefit solutions are introduced during the manufacturing process of the material - be it a coating, a synthetic material or a fabric - and do not require any specific maintenance by the operator.
When it comes to the cargo area, Airbus recommends focusing on the touch points of the ground staff such as controls and handles. Solutions for the cockpit are currently under investigation.
3. How did Airbus test the technologies?
We conducted a broad test programme to ensure cabin material compatibility in terms of chemical resistance, corrosion and of course airworthiness, mainly related to flammability, smoke and toxicity. We identified some additional advantages of the antimicrobial technologies: they do not show an impact on materials compared to UV light, or a risk of corrosion compared to fogging the cabin with disinfectant agents.
After a successful testing campaign the product (depending on the material type) can follow one of two paths:
- It can be introduced in the Consumable Material List (CML) and the Aircraft Maintenance Manual (AMM), mainly applicable for retrofittable add-on solutions such as polishes.
CML reference: Self-Sanitizing - Aircraft interior Polish, Application code: 11LAD1
- It can follow an entire material qualification scheme, mainly applicable for new linefit materials with embedded antimicrobial additives.
4. What about efficacy, durability and skin tolerance?
Of course, we also carefully reviewed the antimicrobial test report of the technologies provided by the manufacturer and conducted by independent, accredited test laboratories. It was key to see significant antiviral efficacy (not only antibacterial) before going further in the evaluations.
To evaluate the lifetime of the products we required a test report proving antimicrobial efficacy after artificial aging to simulate abrasion or ‘wear and tear’ in service, as well as the chemical and mechanical exposure due to regular cleaning cycles.
The reviewed products and their biocidal ingredients are in line with current EU and US regulations for these applications. We also considered potential restrictions on the ingredients, in order to be ready for the future.
None of the products are reported to cause skin irritation. For some products, even dermatological tests were performed in addition, as for cosmetics. Some products are also qualified in the medical and/or food industry or already used in public transport, showing good performance levels.
Airbus continues to follow the development and evolution of the technologies and will not accept any environmental, health or safety risks.
5. How will passengers know if or where these solutions are being used in the aircraft?
A specific challenge is to make these solutions perceivable for passengers, as they usually cannot see the technologies applied on the surfaces. However, perception is key! To address this issue, Airbus is testing its “Clean Space” labelling on surfaces which have been treated with antimicrobial materials. The labels are designed for a consistent approach across aircraft but also throughout the cabin, instead of a patchwork of symbols or pictograms different in each aircraft or module (e.g. in the lavatory and at the cabin seat). We believe this will help increase visibility for passengers on hygiene features, contributing to reassuring them during their flight.
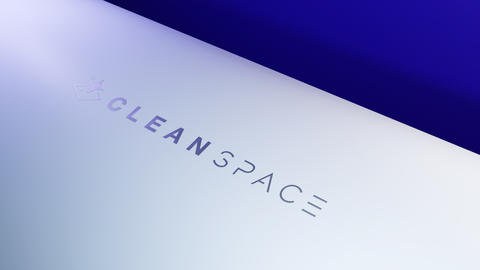
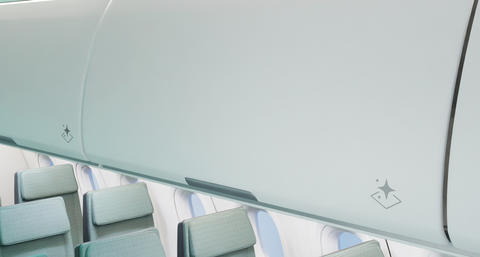
6. Are the technologies meeting a short-term need or are they relevant for the future?
We need to think beyond the current pandemic. Hence, all solutions we have been looking at have a general working principle against microbes, whether viruses or bacteria. Of course, we need to provide a response to the current COVID-19 challenges but we also aim to make the cabin more resilient for potential future hygiene or health risks.
Antimicrobial polishes and surface solutions are recognised by Airbus as a viable cabin solution, enabling airlines to offer passengers a more hygienic and reassuring cabin environment. They tick the boxes in terms of application time, efficacy, tolerance and cost compared to other solutions already tested.
Technology in this field is evolving quickly, and Airbus continues to work with its partners to propose a wider choice of antimicrobial solutions and other hygiene features for their aircraft cabins.
Further reading:
Cabin disinfection, evaluating different technologies
One coating approved by Airbus
Airbus authors:
Andreas SCHÜTT - Cabin Product Manager - andreas.schuett@airbus.com
Mariana ZARPELAO - Industrial Designer - mariana.zarpelao@airbus.com
Other contributors:
Dr. Wilfried MICHAELIS - Expert Environment, Health & Safety - Materials, Processes and Testing
Jens KLÜSENER - R&T Project Leader Antimicrobial materials
------------------------------------------------
Copyright photos and illustrations: Airbus
------------------------------------------------
To view other FAST articles, download the FAST app (available in the App Store and Google Play)