A350F ─ production launch at Aerostructures and Premium Aerotec
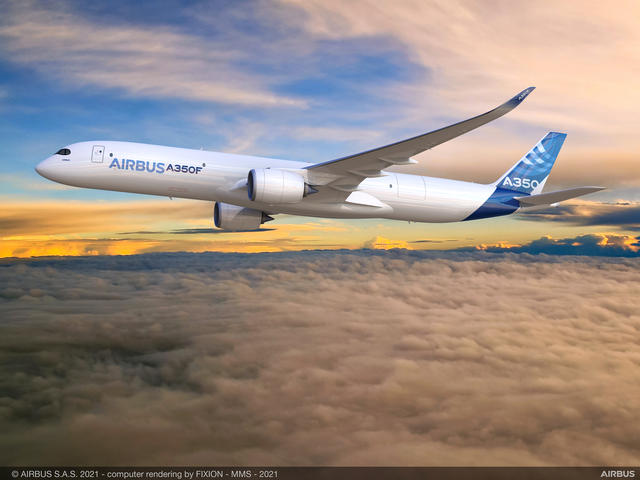
Airbus has received 39 firm orders for the new A350F version since its launch in July 2021. In June this year, the livery of the very first aircraft was unveiled during the Paris Air Show. All that is missing now is the A350 freighter itself.
The aircraft has taken a decisive step forward in recent weeks with the arrival of first components from the plants in Stade, Bremen, and Varel. Airbus Aerostructures and Premium Aerotec (PAI) teams met for the so-called ‘first metal cuts’, although metal was not actually involved every time.
Melanie Markgraf, ASA A350F project manager, witnessed the production starts at Varel and Bremen live. She considers them a special moment on the path to A350F industrialisation. “In 2013, I was lucky enough to celebrate the first flight of the A350, together with many other colleagues” Melanie says. “Ten years later, it is vital to make one of the biggest evolutions of this fantastic aircraft a reality. Every day, a lot of our colleagues work on exciting and challenging tasks to achieve this goal. With the production start at the Bremen, Stade, and Varel sites, we have taken a major step forward together.”
June 2023: kick-off with the lower shell in Stade
At the Stade plant, introducing the A350F will have a big impact on existing fuselage shell production. Additional CFRP (carbon fibre reinforced plastic) bonding jigs will be procured, in particular for the upper shell which will contain a large part of the future cargo door cut-out. The freighter lower shell is, in principle, similar to the A350 passenger version. For its first flight and steep take-off tests, the first A350F will be equipped with flight test instrumentation (FTI), requiring substantial reinforcement of the lower shell’s skin laminate.
The three large CFRP doublers required for this purpose were manufactured by the Stade fuselage shell production organisation using a special process. During the fuselage shell assembly, the doublers will be mounted to the normal outer skin using more than 4,000 additional rivets.
“Since this process would occupy our automated riveting system for a full week and in order to minimise the impact on the series production process activities, we carried out this assembly work with a small team during the summer break” explains Thomas Meyn, industrial project manager at the Stade site“. The employees on the shopfloor and in the support functions were willing to work during the summer break to ensure the start of assembly”.
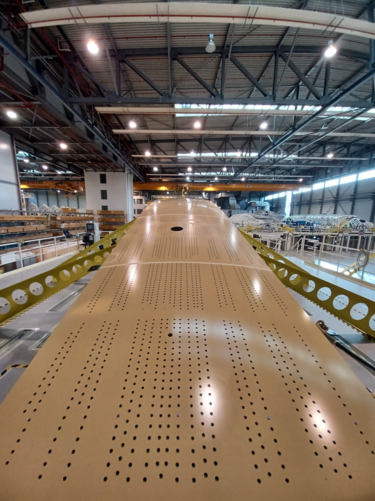
July 2023: first thermoplastic cut for intercostal component in Bremen
The Bremen teams have been hard at work, too. The first component referred to as the freighter intercostal has been industrialised and is ready for delivery. This component is essential for the frame structure of the forward cargo door, which will be subjected to high loads. It is only one of roughly 1,400 components that are industrialised at the Bremen plant and will later be installed in all ASA workshares.
These components are the joining elements between the frames, the skin, and the system connections. Production of the thermoplastic components is one of the crucial factors for the assembly of the freighter.
The Centre of Competence for technological development and industrialisation of complex thermoplastic CFRP components has yet again demonstrated its expertise for the freighter project. This is largely thanks to a high degree of employee engagement at the Bremen site and successful implementation of automated and digitised systems. “The A350F is a great challenge for all those involved, but we will master this one, too”, summarises Norbert Dombrowski, head of ME design consulting.
First metal cut at Premium Aerotec in Varel
Premium Aerotec is responsible for some of the A350F’s major components and is an important supplier to the programme. With the ‘first metal cut’ at the Varel site, i.e. the manufacture of the first machined part, Premium Aerotec has now launched production of this new aircraft type.
Next stop: Nordenham
The detailed parts and subassemblies for section (S) 13/14 will be delivered to the Nordenham plant, where they will be assembled to form a complete section. For S16/18, the individual shells originate from Augsburg and Stade and the floor structure is produced in Nordenham. After the components have been joined in Hamburg to form the complete sections, both will be transferred to the system installation stage.
The first steps of the A350F industrialisation have been taken and the process continues. Melanie Markgraf concludes by saying, “Let’s take advantage of this energy boost to master the upcoming tasks and make freighter history!”
This is the A350F
The A350F is based on the world-class A350-1000. The freighter features a fuselage length optimised for cargo operations and an extra large cargo door on the main deck. Over 70% of the airframe is made from advanced materials, enabling Airbus to reduce the take-off weight by over 30 tonnes for the same mission. The aircraft thus provides an advantage of at least 20% lower fuel burn and CO2 emissions over its competitor product. With a payload capability of up to 111 tonnes (five tonnes more payload and 11% more volume than its competitor), the A350F serves all cargo markets, from express traffic to general cargo, and even outsize loads. In the large freighter category, it will be the first to fulfil the ICAO CO2 emissions standards for 2028.
Coordinated organisation for developing and producing the sections
Aerostructures develops the forward section, whereas the engineering responsibility for the aft section lies with Airbus Operations. Both sections are manufactured in close collaboration between Premium Aerotec and Aerostructures. The forward shells and the main deck cargo floor for both sections come from the Nordenham shop floor, the rear side shells from Augsburg, the rear upper and lower shells from Stade, with Varel supplying the surrounding area of the door for both the smaller forward doors and the large main deck cargo door. Section assembly for S16/18 as well as the general system installation for both sections take place at the Hamburg site.
Your media contacts
Contact us
Bernard De L'Estoile
Freighter Marketing
Valérie Varlet
Comms Advisor A330, Freighter & Cargo
Latest news
Continue Reading
A suite of comprehensive services to keep the A220 flying
Web Story
Aircraft
Like all Airbus aircraft, the A220 benefits from innovative services that facilitate its seamless integration into any operator’s fleet.A350F: what makes the world's largest main-deck cargo door a special one...
Web Story
Aircraft
Airbus confirms Hughes as an additional provider of LEO and GEO services for HBCplus
Web Story
Services
Airbus and Panasonic Avionics to co-develop the future Connected Aircraft platform
Web Story
Services
Airbus and Amazon’s Kuiper team-up to offer LEO satellite network for HBCplus
Web Story
Services