A350 Final Assembly Line gets ready for the Freighter
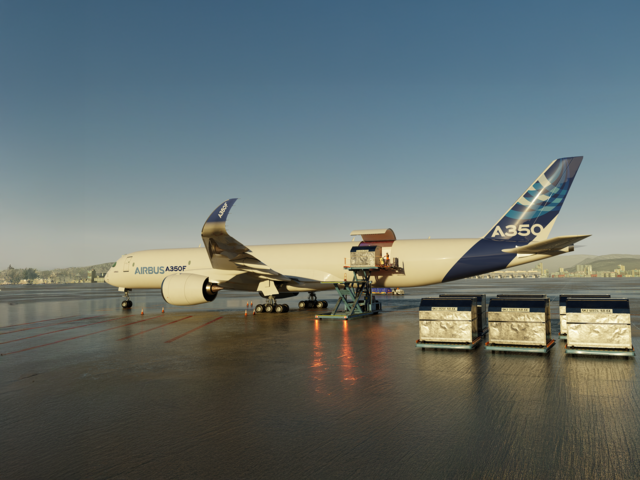
As the first large parts for the A350F take shape at Airbus Atlantic and Airbus Aerostructures facilities in France and Germany, teams in Toulouse are already busy preparing for the final assembly activities which will begin next year. For the latest insights, we spoke to Emmanuel Royer, Airbus’ A350F FAL industrial lead.
Before we explore the details of the final assembly line (FAL) adaptations, it’s worth a recap on how the freighter is different from the passenger versions. Firstly, the A350F is the third member of the A350 Family which shares significant commonality, yet also features various structural reinforcements (such as to the centre-wing-box with reinforced floor beams) as well as dimensional, geometrical and equipment changes compared with the passenger variants.
In particular, the freighter’s optimised fuselage length sits between that of the long A350-1000 and the standard A350-900. The aircraft also features a dedicated large freight door cut-out in the left side of the rear fuselage – the largest main-deck cargo door ever on a commercial aircraft.
Meanwhile, on the inside, the freighter’s floor features a full-length cargo-loading system to support the cargo containers and pallets, and the sidewalls are protected by a windowless lining. There are also major design changes at the front of the interior, such as the 9g cargo barrier wall, on the other side of which is a dedicated flight crew rest compartment (FCRC) and courier area.
Adapting FAL stations for the A350F
For the assembly phase, the new geometrical differences have required corresponding adaptations to the jigs and tools in the Roger Béteille A350 Family FAL – which currently produces the -900 and -1000 versions. Changes are also being implemented to provide production staff with flexible access so they can enter inside the freighter and also reach exterior features – particularly around the large cargo door frame.
In all, eight stations are being retrofitted for Airbus by Ascent Aerospace. Airbus Facility Management is involved too, in the integration task – especially as there are interdependencies with the existing building and its concrete base.
This work, which started during the summer of 2023, has recently been completed (at the end of October 2024). The rest of the jigs and tools for smaller pieces will be ready prior to the arrival into the Toulouse FAL of the large fuselage sections with monuments and other equipment, followed by the wings.
Royer recalls: “The forward part of all our stations – where we want to be freighter capable – had to be modified, so the main jacks and pickup points on the stations were changed. We reworked the concrete, the hardware and the software to accommodate and manage the new fuselage length. Being able to change the jig length globally from one aircraft to another will therefore allow us to be flexible for -900, and -1000 and now the freighter.
Notably, up to now in the FAL stations, there were no aircraft access points at the particular location where there will soon be a cargo door. “We had to transform our stations by positioning special jigs and a tower to allow people to access the main deck cargo door and also permit trolleys into the aircraft through the door,” he explains.
Freighter FAL modification highlights…
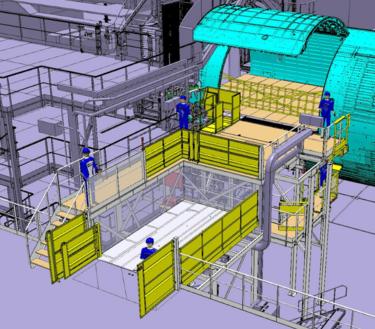
‘Station 50’ in the FAL not only performs the A350 Family fuselage join-up but also delivers various items into the fuselage. The design rendering above shows the new ‘adaptable platform’ for the freighter, which will enable production staff to operate the freighter’s Main Deck Cargo Door (MDCD) and access the fuselage for systems installation.
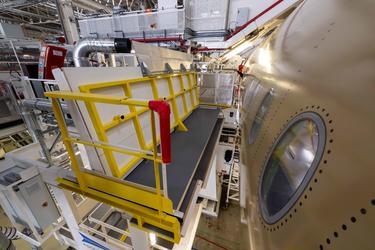
The above close-up image at Station 50 shows part of the new adaptable platform already installed in the A350 FAL.
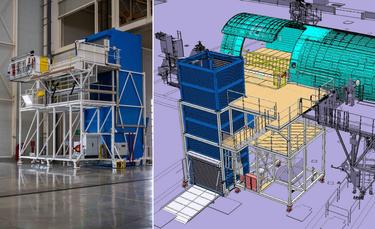
The above image shows Station 40, where the A350 Family’s wing join-up takes place, as well as interior equipment installation. Here a new platform plug is being tested – which would be used when a freighter variant is being assembled at the station. It features a dedicated lift to bring the cargo loading system & cargo lining trolleys as close as possible to the main deck entrance.
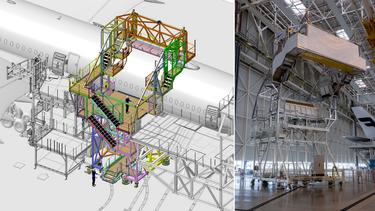
At Station 30, where the A350 Family’s indoor ground tests and interior pre-customisation takes place, the new MDCD platform plug (illustrated above), will enable production staff to access through the freighter door, and more importantly enable rigging and check of the complete door surround. It will allow workers to walk on the top of the fuselage skin, right above the door hinge. That jig is approximately 14m high and is the highest structure in A350 FAL.
Early simulating of the assembly process
In addition to the physical changes already being made to the A350 FAL stations, adaptation to the processes and methods to be used by the production teams is also in full swing.
“We are already using various tools to simulate our flows; to simulate the work sequence and the full sequence of workers doing their activities inside the aircraft,” says Royer.
He adds: “Even before we had our stations transformed, we created the digital twins that allowed us to explore and refine our FAL scenarios, regarding our resources, materials, time organisation of the work. Typically, such simulation would help us to define in advance how best to install the Ancra-supplied cargo loading system (CLS) and cargo linings provided by Vaupell.”
Taking the latter as an example, the FAL teams will have to install into the aircraft each and every part of the CLS. This amounts to more than 3,000 detailed parts including rollers, latches and power drive units (PDUs) during the FAL flow. Moreover, the parts must be directly integrated onto the floor grid, ie. embedded into the primary structure. This is a change compared with A330-200F for which the CLS components (eg. roller trays and ball trays) were installed to intermediate structural adapters.
While this all sounds quite labour-intensive, the teams will benefit from the ‘digital continuity’ approach whereby augmented-reality solutions would display to them – via 3D ‘HoloLens’ glasses – the parts they need, the operations to follow, and good locations to install them on the aircraft.
Furthermore, to help this all to run smoothly from day one, a task force is also preparing the content of the awareness sessions and contributing to the creation of future training courses for the production group to prepare the FAL teams for the arrival of the freighter.
Co-design and co-development
A key approach applied to the activities since the launch three years ago is the co-design and co-development of the aircraft. “We have been defining the different technical solutions together with our colleagues in the Airbus Design Office, to attach and connect the different parts; And to secure the detailed design of these parts and subsequent industrialisation.”
For example, for the FAL to be ready to install and integrate the 9g barrier wall, the FAL team is co-designing it together with Airbus Engineering and Turkish Aerospace.
This part will be installed in a single piece thanks to a mini lifting system and a trolley specially designed to accompany the process.
“We are really part of the development team of this component to make sure it fits with our industrial constraints in terms of ergonomics, safety, lead time for installation, and our competencies,” says Royer.
Likewise, for the main-deck cargo door and the cargo lining and all the different freighter specificities, whether it is on the product design, installation the test strategy of the aircraft, the teams are co-designing the product.
“This approach started at the launch of the programme, but really in the last 12 months the freighter teams have been in ‘sprint’ mode to close most of them during 2024 and thus help with the detailed design freeze of the various components,” he adds.
Defining ground testing strategies
The ground test design was involved very early on in the A350F development cycle, in close collaboration with all the design offices as well as the “Chief Engineer” teams. In this way the testing work stream also used the ‘co-design’ approach to ensure that the testability constraints of the FAL systems are taken into account in the up-front design of the aircraft. This covers the following areas: safety, ergonomics, accessibility, test strategies, feedback from the -900 / -1000 and A330F programmes, simplification and standardisation of resources, and optimisation of cycles.
One practical advantage of this resulting testing strategy during serial production is that it will help the A350 FAL teams to be able to switch from freighter to passenger and vice versa with as minimal disruption as possible.
“Taking the CLS again, this installation would be tested much more than what we do on the lower decks of passenger aircraft today,” notes Royer. “This full end-to-end system needs to be physically tested with some pallets and loads as if we were an airline. We will also need to test all the functionalities of the loading system,” he explains.
Looking ahead
Summing-up the current status and next steps, he says: “As well as finalising the readiness of our jigs and tools over the next six months, we will also finalise all the instructions and work orders to prepare our teams, train our workers and to secure that everybody is ready with everything in place for the A350F FAL start.”
Your contact
Martin Fendt
Airbus Corporate Communications - Airbus Commercial Aircraft