First A350F: Engine pylons and tools are in production
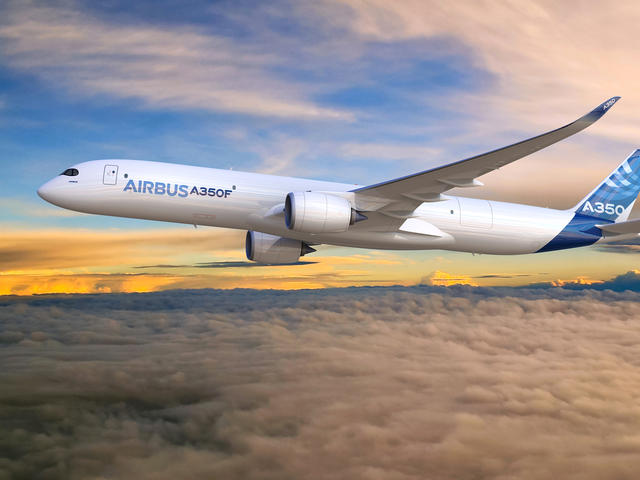
Final assembly of the A350F, the freighter version of this aircraft family, begins this year. All Airbus industrial sites are working hard in their specialties to rise to the occasion. Teams on the A350 assembly line in Toulouse are ready to receive their various components. In 2024, other sectors in Toulouse faced innovative challenges, such as those related to tools, engine pylons and the first 'Metro'.
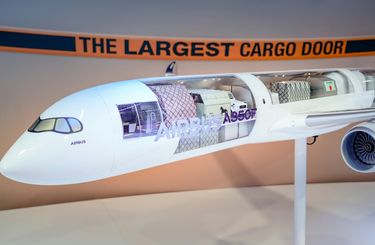
The majority of Airbus engine pylons are manufactured at the Saint Eloi site. This titanium component connects the wing to the engine and withstands temperatures from -50° to +600°C. For the A350F version, the MFT in charge of machining and assembly had to take into account the stiffening of the two engine pylons, with reinforced sizing of certain parts and fasteners, as well as the design of a new cowling.
Christophe Hazanbegovic, A330/A350 VSM representative on the project, said: "The close working relationship with the Engineering, Methods and Production teams was a major factor in the project's success".
Another new feature of the very first A350F pylon (MSN700) is the integration of a new generation of optical fibre. Optical technology has already been present at Airbus for several years. It was introduced on the A380 to transmit information. For the most part, this is the domestic optical fibre that everyone is familiar with. "This new generation of optical fibre is capable of considerably improving the detection of overheating around the engine pylon's insulated air pipes, and reducing parasitic signals. It's a big step forward," commented Quentin Allard, industrial project manager for St Eloi.
Unlike domestic optical fibre, this fibre is thicker and more resistant. Installation by the operators went smoothly. "After several installation tests and this first installation, I'm confident about the introduction of this new technology," said a system operator involved in the Saint Eloi project. "The challenge is to ensure that the bending radii are correct and that the connectors are clean. The route is entirely new, but no more complex than the old system. After installation, we have to carry out checks to certify the conformity of the optical system".
With the help of the Electrical Methods Department, the installation of this new fibre was a success. The time spent on this installation is identical to that on the old system. Optical fibre installation and connection exercises are underway in the Saint Eloi Training Room. Installation of the left and right engine pylons is currently being finalised, for delivery this year, on an A350 FAL Station 40.
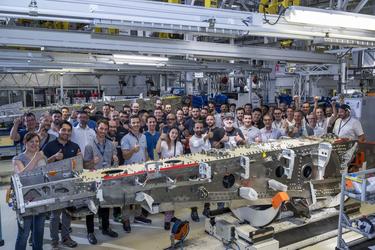
At the Saint Martin site, the proudest achievement of the FAL Industrial Support Tooling teams is the adaptation of certain A350 FAL assembly stations to integrate the specific features of the A350F. Such is the case with the 'Godzilla', a tool unique to the Toulouse sites.
"This 14-metre-high, 14-metric-ton metal monster is unique in that it provides access to the cargo door, allowing operators to move around and work on the upper fuselage in complete safety and ergonomically," said Jérôme Fraysse, project manager. "The aircraft environments of our assembly stations currently move on rails. With the 'Godzilla', this was not an option. So we turned to a new, hitherto unused technology: motorised wheels guided by lines on the ground and QR codes. The new accesses to the largest cargo door ever installed on the main deck of a civil aircraft, are controlled by a wireless remote control. This, too, is an achievement of the Cargo project team!"
And this is where the genius of Airbus employees comes into its own. They thought, if we can motorise this new equipment, why not adapt the current A350 tooling with robots on wheels? Today, robots interface with certain jigs at Station 50 and manoeuvre them safely through the stations and inside the aircraft, saving precious time in the industrial cycle. For Romain Peyrola, A350 Industrial Operations Means: "Other challenges were taken up by the teams. The MFT (Manufacturing Engineering, Ergonomics, HSE teams) has integrated changes in aircraft design, taking ergonomic aspects into account to facilitate operators' work and ensure their safety. But also to fit our interventions into the production schedule to carry out the work. When a station was available for a few days, the teams prepared as if for a marathon, in order to optimise the effective intervention time of the various parties involved (industrial resources, facility management), without disrupting aircraft production and delivery".
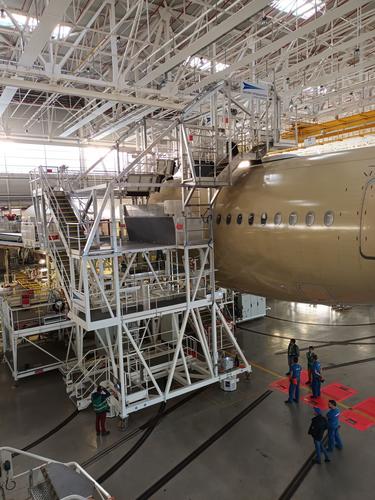
This year, when assembly of the first A350F begins, the jigs and tooling will be able to receive all the industrial components from the Airbus production sites. The two engine pylons, assembled at Saint Eloi, will be delivered directly to FAL Station 40 and installed under the aircraft's wings.
Another A350F victory: The Toulouse Electrics Centre powers up the first "Metro"
At the end of the year, a major milestone was passed by the Toulouse Engineering and Electrics Centre teams with the power-up of the first A350 freighter 'Metro'.
This new assembly, fitted with the main Flight Test Instrumentation (FTI) systems, will shorten the aircraft integration phases and enable functional checks to be carried out as early as possible before installation on the aircraft, thus limiting the impact on the A350 assembly line schedule. The Metro also features an innovative Flight Test Engineer Station (FTES), essential for future flight test campaigns. Manufactured 100% in-house by the Electrics Centre's experts, this assembly weighing almost 1.8 metric tons required more than 1,600 work hours from Manufacturing Engineering and 2,700 work hours from Production.