Over 15 years, the A350 will incur 25% less maintenance costs
From the start, meeting our customers’ expectations in terms of fleet management and operational performance has been top of the agenda of the A350 programme. As a clean-sheet design, the A350:
- Has the most simple, reliable systems
- Uses optimal, advanced materials
- Requires fewer maintenance tasks and has longer check intervals
- Is powered by the most efficient aero engine
so as to maximise the reliability of the aircraft and its availability for revenue flights whilst making substantial savings.
Simplified systems
Other than fuel, maintenance is the highest Cash Operating Cost component. The A350 is designed for lower maintenance costs, with efficient systems using simpler architecture, fewer parts and higher reliability.
An example of this simplification is the A350’s 2-circuit, 5000 psi hydraulic system. Replacing the more conventional three circuits operating at 3,000 psi found on most other aircraft, this simplified architecture contributes heavily to reducing maintenance costs by significantly reducing the number of parts in the system. Reliability is improved and the risk of leakage reduced because there are fewer lines. This, and the fact that the pipes, hoses and actuators are all smaller also contribute to lowering aircraft weight, and so fuel burn and emissions.
Fewer maintenance tasks
The A350 reduces maintenance cost not just through simplification of system architectures, maintenance procedures and reductions in spares holdings, but also by removing tasks and extending maintenance intervals.
Across the airframe, the choice of the most appropriate materials eliminates, where possible, the risk of corrosion and reduces the requirement for fatigue inspections.
For example, the A350’s landing gear uses titanium to extend Time Before Overhaul. The A350 has a 12 year TBO at EIS with a further target of reaching 14 years.
In addition to titanium, which accounts in all for some 14% of the A350’s structure by weight, the aircraft makes extensive use of composites. These account for 53% of the A350-900’s structure. This means that no corrosion tasks are required for almost 70% of the aircraft structure, and no fatigue tasks for the 53% of composites.
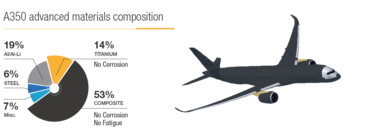
Connected to optimise maintenance scheduling
The A350’s On-board Maintenance System (OMS) provides both a diagnostic function via the Centralised Maintenance System (CMS) and a prognostic function via the Aircraft Condition Monitoring System (ACMS).
The CMS identifies system failures, centralises data from the Built-In Test Equipment (BITE) of the various aircraft systems and creates standard or customised fault reports.
The ACMS acquires and processes aircraft operational data in order to reduce scheduled maintenance and support operators in performing preventive maintenance. It provides operators with performance and trend information about the aircraft’s systems and engines.
Gathering huge amounts of data – more than 20,000 standard parameters – the A350’s ACMS is THE Skywise enabler for health monitoring and predictive maintenance.
Highly reliable engines
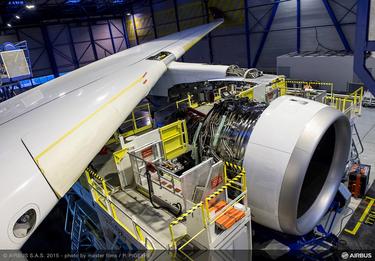
The A350 is powered by the world’s most efficient large aero-engine flying today: the Rolls-Royce Trent XWB. Having experienced the best entry into service of any Trent engine, the Trent XWB has now accumulated over 11 million flight hours at an exceptional 99.95% operational reliability.
The unique three-shaft design of the Trent reduces load flexing in the turbine and results in superior engine performance retention as well as better reliability and durability (time on wing).
The three-shaft layout also allows the fan to be positioned the optimum distance from the core to improve FOD (foreign object debris) deflection into the by-pass duct, further protecting the core.
Benefiting from the latest available technologies, the Trent XWB is not only a highly reliable, durable, low maintenance cost engine but also offers lower fuel burn, emissions and noise than comparable engines.
Conclusion
The A350’s clean-sheet design is based on efficient systems using simpler architecture, fewer parts and higher reliability. Across the airframe, the choice of the most appropriate materials eliminates, where possible, the risk of corrosion and reduces the requirement for fatigue inspections.
Overall, the A350-1000 has been designed with the aim of significantly reducing maintenance, increasing overall aircraft reliability and minimising downtime for scheduled and unscheduled maintenance.
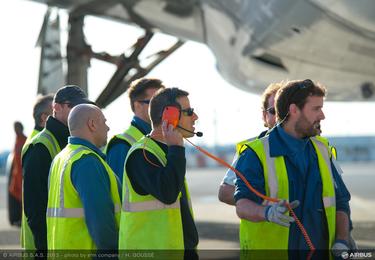