End-of-life Reusing, recycling, rethinking
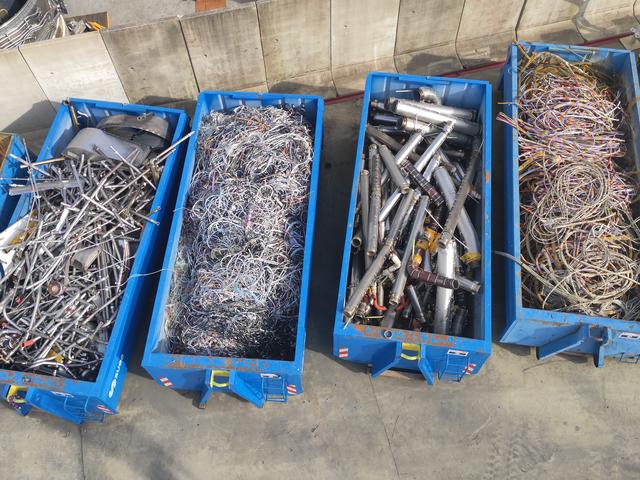
Have you ever wondered how much recycled material is used in the building of Airbus aircraft and how much of the aircraft can be recycled?
Reusing and recycling have been part of this industry for years. However, with today’s spotlight firmly focussed on sustainability, aviation must deliver noticeable results, show engagement and sometimes even completely rethink materials and ways of working.
What options should operators consider today for an aircraft at the end of its flying life, and what is around the corner for becoming even more sustainable?
Why managing end-of-life makes sense
Operators have several options when considering the next steps for an aircraft.
One of these is to extend the flight hours or cycles limit of the aircraft thanks to “extended service goal” upgrades.
https://aircraft.airbus.com/en/services/enhance/systems-and-airframe-upgrades/operations-extension
Alternatively, reusing parts from an aircraft or recycling materials both offer financial benefits. There is still significant value in an aircraft’s components and its metallic materials, even at the end of its life. So it makes financial sense for operators.
Aircraft can also be repurposed for training, or even showcased in a museum.
It is the owner’s corporate social responsibility to properly manage the end-of-life of their aircraft.
Ensuring used parts are safe and certified
An aircraft owner might already be sourcing Used Serviceable Material (USM). This can be an efficient alternative to new parts, in particular during times of tension in the supply chain.
But the aircraft owner can also source USM from their decommissioned aircraft and use them after repair and recertification. They can sell these parts to a broker or a material expert like Satair.
Nicolai Hertz, Head of Used Serviceable Material at Satair*, talks about USM from the customer’s perspective.
Q1: As a customer, what should I be looking out for when considering used serviceable material?
When buying USM it is essential to ensure that you are getting the right release certifications. These may be EASA, FAA, DUAL RELEASE, or any certification required, based on the origin of the previous customer. In addition, you need to obtain the proper shop reports from approved repair shops, proper traceability, and in many cases a Non-Incident Statement (NIS). All of this should of course be coming from a trustworthy, reliable and reputed provider to ensure that documentation is authentic and safety requirements are met.
Q2: What do customers expect when buying used serviceable material?
As with any purchase, customers expect a smooth buying experience with competent service from the provider. This means getting quality USM with full traceability and all the required certifications.
Sourcing new parts in 2022 has become a real challenge due to raw material and transport shortages, plus rising energy prices. This means that longer lead times for repairs and new material continue to affect customers, who then choose to look for alternative options to secure their material needs. As a result, the demand for USM is increasing, particularly within the single-aisle market as buyers seek to satisfy their demand for low-cost, USM options and increasingly see it as a viable option to support deferred engine maintenance post-covid.
*Satair: An Airbus subsidiary, providing material management and service needs for the civil aerospace industry. https://www.satair.com/
What is recyclable?

Once the owner has decided to phase out an aircraft, a specialised company needs to decommission it. This involves aircraft owners, brokers, MROs, dismantlers and recyclers.
The first steps will be to remove the valuable components selected by the owner which can be repaired, overhauled and recertified in order to fly again as Used Serviceable Material (USM).
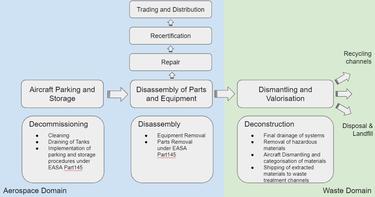
By “recycling” in this article, we refer to what can actually be recuperated back to raw material and transformed for other uses. Recycling an aircraft requires expertise not only about the aircraft, but about the rules and regulations in force as well as safety considerations for handlers and the environment.
Alexandre Brun, CEO Tarmac Aerosave* gives an insight into how it works and what can be recycled.
Q1: How does aircraft recycling work?
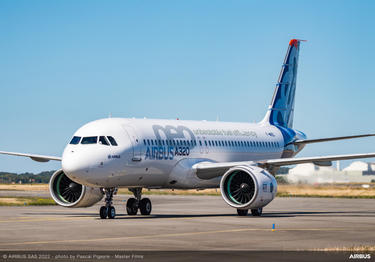
We have a recycling process that meets strict environmental regulations. First, the aircraft or engine equipment is removed by qualified personnel in accordance with the manufacturer's guide provided by the owner. Removed parts are then reconditioned and re-certified so they can be returned to the after-sales market.
Once all the requested equipment has been removed, we disassemble the aircraft, and remove all its components (electrical, hydraulic systems, etc.) to be able to start cutting up the fuselage without any risk. The windows, for example, are of interest to the interior design industry, while the plastic elements are used to create clothing or fleece blankets.
This way, 92% of an aircraft's total weight and more than 99% of its engine parts (CFM) is recycled by Tarmac Aerosave. In the case of A320 aircraft, 92% of the total weight of the aircraft is recovered. The A320’s airframe is composed mainly of aluminum and alu-Li alloys (72%) steel (9%) and titanium (6%). All these metals are recycled at the end of the aircraft’s life. They will be valorised by specialised channels and once melted will be used to form new parts for non-aeronautical applications.
Composites and other materials can be used for energy recovery or disposed of in compliance with local regulations.
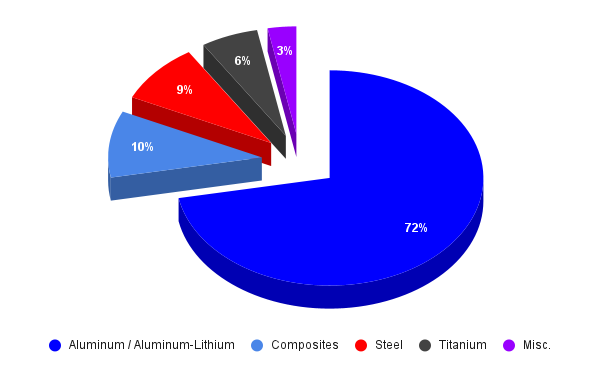
Q2: What are some of the challenges of recycling?
Airframe disposal requires processes to be respected, careful handling, and precise documentation.
There must be, for example:
- a process which is fully compliant with strict European legislation,
- traceability of removed parts,
- ISO 14001 and EN 9110 certification,
- dedicated, waterproof recycling areas with a water collection and treatment system,
- a wire-saw cutting process avoiding hot points and mixing of materials,
- a secure handling process of cut parts, protecting handling workers,
- optimized sorting of all materials.
The challenges of recycling are now to remove barriers to enable the use of recycled materials in the production of new certified flying parts, to prepare the eco-system and to anticipate the recycling of tomorrow's waste, such as carbon composites.
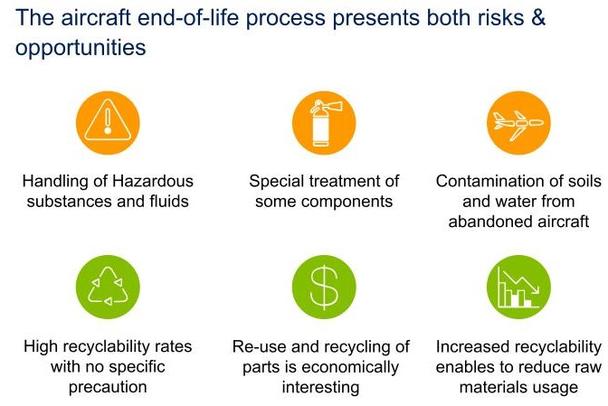
Airbus' role in the value chain
As an aircraft manufacturer and part of the value chain, Airbus promotes responsible capabilities and practices associated with the recycling of its aircraft, with particular focus on 3 areas:
- Prevention. This covers avoiding degradation of end-of-life performance, encouraging incremental improvement and implementing eco-design principles.
- Re-use. This means looking at improving repairability.
- Recycling. This involves:
- improving traceability of substances and materials all along the product life cycle,
- contributing to the development of new recyclability channels and technologies,
- supporting the use of recycled aeronautical materials into new aircraft manufacturing
- developing upcycling and downcycling value chains with partners.
Continuing to drive recycling
Back in 2007, the Tarmac Aerosave company was created for sustainable dismantling of commercial aircraft. It was a result of the Airbus-coordinated PAMELA project (Process for Advanced Management of End-of-Life Aircraft).
More: https://webgate.ec.europa.eu/life/publicWebsite/index.cfm?fuseaction=search.dspPage&n_proj_id=2859
Airbus and Tarmac Aerosave are now looking at how to further increase the value of material at end-of-life with sorting into specific material classes. They are also working with the ecosystem to bring some materials back into the aerospace supply chain, as primary or secondary structures, while other materials will continue to feed the wider industrial market.
Composites
Meanwhile, materials have been evolving for the latest generation of aircraft with, for example, the introduction of composites. Indeed, the A350 is over 50% composite. Composites have contributed to improving aircraft performance thanks to their light weight. The next step is to look at recycling it.
In order to anticipate future end-of-life management of composite aircraft, Airbus initiated early 2022 a new European project, focusing on dismantling and recycling of large composite structures. HELACS (Holistic processes for the cost-effective and sustainable management of End of Life of Aircraft Composite Structures) comes under the Clean Sky project.
Second-life services in China
During their life aircraft undergo maintenance, upgrades, checks and maybe short or long-term pauses in operations. This is all before the final stage where end-of-life options need to be considered. Professional, quality aircraft care during any of these periods is essential, whether to ensure safe return to operations or to maximise end-of-life financial returns.
Regional lessors and operators of commercial aircraft in China and surrounding regions will be able to address their requests to a new set-up in China. The future Airbus Lifecycle Services (ALS) Centre will provide a wide range of second life services for commercial aircraft. The resulting Used Serviceable Material (used parts) will be sold and distributed by Airbus material management subsidiary Satair with priority given to lessors, airlines and worldwide MRO’s Brokers (USM).
Managing end-of-life makes sense, financially and environmentally, for both operators and manufacturers. However, ensuring it is managed safely and according to stringent industrial requirements can be more difficult. Operators requiring comprehensive services to meet their needs can turn to companies such as Tarmac Aerosave and Satair and, in the future, ALS in China.
Significant progress has been made over the years to reuse and recycle but it does not stop here. Airbus and its partners are continuing to seek new solutions and this includes rethinking materials right from the design phase.
Meanwhile, the evolution of climate-related laws and initiatives shows a clear move towards product circularity to support climate-neutrality targets.
Your media contacts
Contact us
Loic Dunand
Head of Lifecycle Programme
Latest FAST articles
Continue Reading
Getting ready for A350 cabin retrofits
Web Story
FAST
The first A350s are reaching eight years in service, and the wave of cabin retrofits which is now starting will rapidly gain momentum over the next few yeaTurbulence alert - The collaborative network
Web Story
FAST
Intermittent repetitive failure
Web Story
FAST
End-of-life Reusing, recycling, rethinking
Web Story
FAST
In-flight health monitoring
Web Story
FAST