Getting ready for A350 cabin retrofits
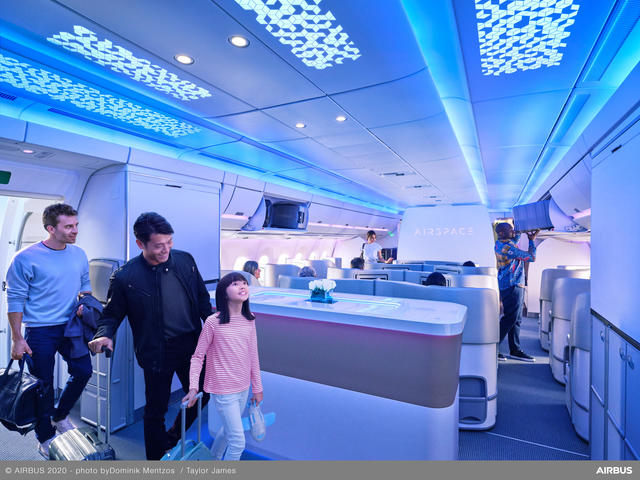
The first A350s are reaching nine years in service, and the wave of cabin retrofits which is now starting will rapidly gain momentum over the next few years. This three-part article discusses: the current drivers for the impending wave of A350 cabin upgrades and product enhancement opportunities for airlines; the upgrade learning curve and technical considerations relating to the A350’s 3D design approach; and a detailed look at the various stages of the customer’s joint project journey which they will undergo together with Airbus Upgrades Services – from initial planning to completion.
PART 1 – Market drivers for A350 cabin upgrades
Since 2014, almost 600 A350s have been delivered and Airbus is anticipating the first wave of cabin retrofits – which typically occur on aircraft that reach eight years of service. By 2028 there will be around 390 A350s that will have reached this age. Typical upgrade drivers for airlines will include: interior rebranding; class segmentation; seat-count optimisation; as well as harmonising their in-service products to match those of the new aircraft joining their respective fleets.
To be prepared to meet this steep ramp-up, Airbus Customer Services has set up a dedicated project encompassing all dimensions of this challenge, with a team of experts ready to provide airlines with more details as they plan to upgrade their A350 fleets and thereby enhance their assets’ operational value and passenger appeal.
Airbus is also increasing its internal capacities within retrofit Engineering and Programmes management. Suppliers have already been informed and Airbus is reviewing the industrial capacity and competitiveness of the supply chain. In addition, Airbus is studying potential partnerships with third-party aftermarket providers to develop complementary offerings to meet customer expectations.
Enrichment of the A350’s cabin catalogue since EIS
Airlines can today consider a range of additions to the Supplier-Furnished-Equipment (SFE) cabin equipment catalogue items – which were not originally available at the time of the A350’s cabin definition freeze in the early 2010s. These typically include new types of lavatories, galleys, ovens, fridges, chillers, beverage makers, trash compactors, electro-dimmable windows etc..
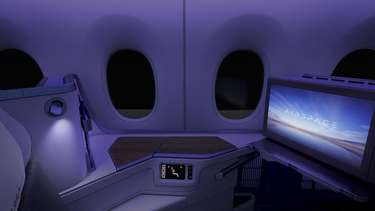
There are also new types of buyer-furnished equipment (BFE) to consider – including business and economy class seats and new types of in-flight entertainment (IFE). For example, from 2020 Airbus offered 4K IFE versus the existing 1080p screen definition.
As the chart below shows, Airbus has developed and progressively enriched its wide-ranging and tailored catalogue of retrofit BFE and SFE cabin products for customers, applicable to their particular A350 production standard and configuration. The full range and their potential retrofitability for a specific customer’s aircraft can be fully explained through their assigned Airbus Services Sales Director.
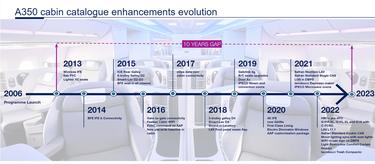
New built-in SFE satellite connectivity solution
Airbus is offering as SFE (both in retrofit and linefit) its built-in high-bandwidth connectivity platform, known as HBCplus. With this flexible satcom solution, the antenna and modem hardware are fully integrated as an SFE product by Airbus. This approach enables in-flight connectivity directly from multiple satellite constellations, via a choice of network providers. By contrast, previous connectivity offers were only provided as part of a bundle with IFE and the BFE hardware, thus any change of the service provider would require a change of the hardware.
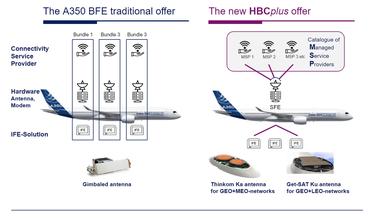
Examples of typical A350 & Widebody airliner cabin retrofit trends
From the operator perspective, some general trends and OEM cabin-related offerings for large airliner cabin upgrades are observed across the industry. Some examples of these are summarised below:
- Business Class – demand for more privacy features: A current trend is the installation of Business Class seats – or ‘mini-suites’ – with sliding doors. The A350 can offer these with four-abreast direct-aisle access, with arrangement in either herringbone (angled relative to the aisle) or staggered (parallel to the aisle).
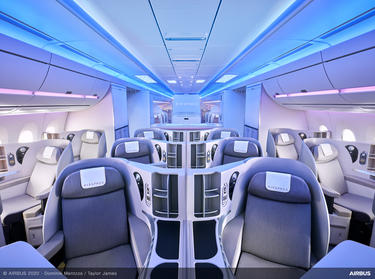
- Premium Economy Class – gaining popularity: Airlines are choosing to retrofit premium economy (PYC) where it was not originally selected in line-fit. And where the operator’s aircraft already had PYC, some are extending its proportion in the cabin. In the A350, PYC is typically accommodated in an eight-abreast layout, with a pitch of around 38 inches (versus nine-abreast and 31-32 inch pitch for regular Economy class).
As well as lower ticket prices compared with Business Class, PYC also reduces the associated CO² emissions per passenger per square metre – which are approximately half of those in Business Class.
A typical example of a PYC cabin upgrade was recently performed by Airbus for ITA Airways, to harmonise the cabin experience of the customer’s in-service A350s with that of its new A330neos.
- Economy Class – increasing floor space efficiency: Typical economy class in A350s is the standard nine-abreast with an efficient pitch between 31 and 32 inches and seat width of 18 inches. Airbus has also developed a more optimal 10-abreast configuration for the latest versions of the A350 being delivered which feature a slightly wider wall-to-wall cross section.
- Lavatory trim & finish refresh is a ‘quick-win’ for maximising passenger perception, and thus airlines typically include it during their cabin upgrades. On the A350 an option exists to introduce a more floor-space efficient lavatory which Airbus calls “Smart Lav”. Its smaller footprint brings tangible layout benefits such as a seat-count increase.
- Galley inserts (GAINs): Apart from cleaning and ‘wear & tear’ repairs as required, GAINs are usually unchanged during a cabin retrofit.
- Passenger comfort features: Optional passenger comfort features, such as light-restrictive curtain headers, electrically dimmable windows etc. are available for the A350 and would typically be considered. A350 Customers can also upgrade their customisable ‘mood’ lighting scenarios for passengers and/or to convey new branding etc., easily via software updates.
- The latest In-Flight Entertainment & Connectivity (IFEC) technologies: The IFEC landscape and supply chain is constantly evolving and airlines strive to offer the latest IFEC technology convenience for their passengers.
PART 2: New-generation A350 learning-curve considerations for cabin retrofits
Since the A350 is still a relatively young aircraft, Airbus and the airline industry are still on a learning curve with regard to retrofit of the cabin upgrades. In particular, regarding the capacity needed to reach the required knowledge and maturity as we see on the A320 and A330.
The A350 complies with stronger certification requirements and increased safety for its new weight-saving composites, and advanced metallics – which also enables an optimised primary structure to confer fuel efficiency and long-range performance and economics for its customers. Moreover, new certification which adheres to EASA’s “Certification Specifications and Acceptable Means of Compliance for Large Aeroplanes” CS-25, leads to more stringent requirements which can influence the lead-time and cost of a cabin retrofit.
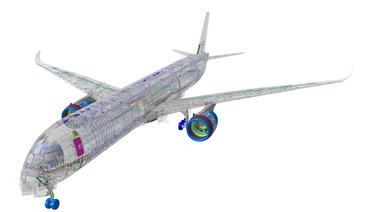
Migrating from 2D design processes to 3D Digital Mockup (DMU)
Another learning-curve factor is the A350’s use of a Digital Mock-Up (DMU) for the entire structure, including the cabin. In practice, the DMU concept describes the entire aircraft design in 3D throughout its lifecycle, including for design upgrades and modifications. This helps to design the upgrade and, for example, not only show the customer how their proposed new cabin layout will look in 3D, but it also allows engineers to delve within the structures and below the floor, or in the ceiling crown area etc, so they can define best routing for pipes or cables to avoid clashing with surrounding structures. For the subsequent Service Bulletin (SB) the 3D output from the DMU is converted into 2D for design certification and for the MRO to plan the embodiment and produce the job cards.
Another benefit of the DMU is that it helps to manage the updating of the aircraft’s technical documentation in the digital domain. This includes all the manuals including the structural repair manual (SRM), aircraft maintenance manual (AMM), illustrated parts catalogue (IPC), etc.
A350 design evolutions and ‘mod-stacking’ implications
The A350’s unprecedented pace of product evolution has resulted in successive production batches – or as Airbus calls them: “Steps”. These have included enhancements to the cabin, avionics, aerodynamics, the airframe structure, weight savings, and so on. Notably, if an airline buys A350s from the recent ‘Step-7’ or ‘Step-8’ batch standards, those aircraft would feature a slightly longer and wider cabin, as well improved aircraft performance thanks to a new aerodynamics package and also weight savings to the fuselage and wings.
Of course, if an airline with new Step-7s also has older A350s in its fleet from an earlier iteration, and wants to harmonise the cabins across all its A350s (the in-service and the new ones) then it won’t simply be a case of copy-pasting the same seats and monuments that are in the Step-7 cabin across to the earlier models, especially since the cabin floor, seat tracks, seat-to-seat cabling routings and sidewalls etc. are physically different.
Moreover, even within a step, there may be differences between one customer and another – which may also require intermediate modifications. The general term governing which modifications are needed as a prerequisite is called ‘mod-stacking’. Overall, as more and more upgrade ‘mods’ are certified, they are re-enriched back into the DMU for subsequent A350 production standards. They are also added to the ‘ready-made’ bank of design solutions to be available as required for future upgrades of in-service aircraft.
Third-party STC modification impact in OEM Upgrade Service Bulletins
Additional complications can arise if the aircraft on which the new mod is to be applied contains any prior modifications which had been implemented by a third party using their own Supplemental Type Certificate (STC), and moreover, these mods were not incorporated into Airbus’ own DMU for that aircraft. Therefore, before Airbus could upgrade the affected zone, a prerequisite is that it would first need to be brought back to the original configuration – ie. ‘as delivered’ by Airbus.
For this reason when an airline comes to Airbus enquiring about a potential upgrade, often the first thing they are asked is whether they have applied any STCs by third-parties on their aircraft. This is because Airbus cannot certify nor provide support for somebody else’s STC to perform a mod on top of it. Nevertheless, Airbus is ready to support if the customer has a qualified ‘design-organisation-approval’ (DOA), by sharing its technical data and IP on a case-by-case basis – which would be a chargeable service.
PART 3: The customer’s journey
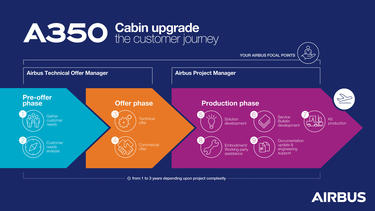
Lead-time considerations
Depending on the scope of the proposed cabin upgrade, customers should budget around one year between their kick-off meeting with the selected provider and the start of the embodiment working party. And that’s a minimum. In some cases – for the more complex cabin upgrades, especially if new seats need to be designed and qualified, there can even be as much as a three-year lead time.
The general consensus is for airlines to plan their cabin upgrades during a C-check, in order to leverage the downtime and minimise the impact on operations – which is roughly one month. However, if the upgrade requires a longer duration, then one approach could be to perform it during the winter, or ‘low’, season. It also depends of course on the MRO availability in terms of slots.
The Service Bulletin authoring phase can typically start some six to nine months before embodiment. During this time Airbus will be in close liaison with the customer to ensure there will be no structural, systems clashes or other ‘surprises’ once the aircraft arrive and the kits are delivered.
When these SBs are finalised and approved, they are delivered by Airbus to the MRO around one month before the first kits arrive from Airbus’ dedicated logistics centre in Hamburg, Finkenwerder, and the customer’s aircraft enters the working party hangar. This is the approximate time needed for the MROs production planners and manufacturing engineers to study the SBs and prepare the work sequence and the associated job cards.
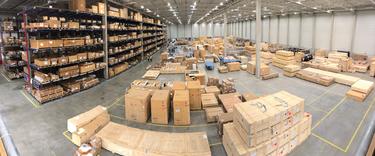
The development, qualification, manufacture and delivery of new seat models – especially if an airline wants to have brand new business class seats – can add up to 36 months to the ‘critical path’ in terms of the overall project planning and lead time. Furthermore, where new seats, new trim and finish and new monuments are involved, then the associated engineering integration activity will also influence the lead time. This integration work is needed to really study how to translate the results into the approved SBs.
Preliminary groundwork for the customer’s Requests For Proposals (RFPs)
Once the airline or operator has decided internally to proceed with a cabin upgrade, and has determined the lead-time considerations (such as those described above), it will be able to launch preliminary feasibility discussions with external partners, MROs, vendors etc. During these early discussions the operator will draw-up the concept – including the “Layout of Passenger Accommodation” (LOPA), “Rough Order of Magnitude” (ROM), due dates etc.. The customer will also need to pre-determine available MRO & hangar slots.
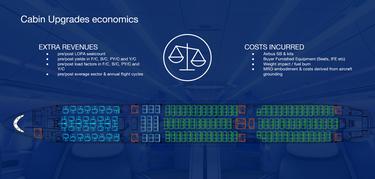
During this exploratory phase, the airline will work with Airbus Upgrades Services on defining the post-mod LOPA long before the SB design can be finalised. Also known as the “Aircraft Interior Control Document” (AICD), the LOPA is essentially the engineering diagram which outlines the aircraft’s cabin interior which includes, but is not limited to, locations of passenger and crew seats, emergency equipment, lavatories, galleys and the exits.
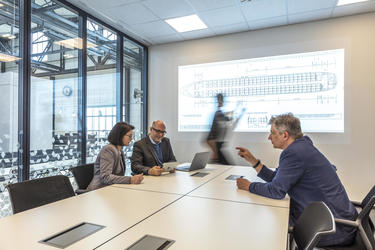
Many customers already have a good initial idea of what they want to implement post-mod and LOPA. They are typically the ones who have performed this part themselves – including defining all the seat counts, passenger profiles. Then they need from Airbus the ‘rough order of magnitude’ or “ROM” quote. Some airlines are open to Airbus’ suggestions and proposals – which can take time – maybe up to six months to define the LOPA.
The preliminary phase helps to ensure that the RFP already takes into account the feedback from potential providers, and will not therefore require further re-drafting, thus paving the way for a smoother tender response phase from the prospective providers and final down-selection. Once all the items have been approved by internal management, the operator will issue its formal RFP to the prospective external providers.
As well as the usual specification, lead-time and pricing criteria, the customer’s RFP should also place an emphasis on the prospective provider (ie. Airbus or a third-party) having strong project management and workforce in place, and to show proof of their ability to monitor and control their suppliers’ deliverables and of the EASA certification plan. These are essential capabilities that will help the project to proceed on time, on quality and on cost as specified in the contract.
Upgrade providers’ response: Commercial & Technical Offer
From Airbus’ perspective, once it receives and subsequently analyses that RFP, it will be in a position to provide the ‘Commercial Offer’ to the customer. This offer will confirm all the details such as firm pricing, escalation rules, milestones planning etc. The latter will include the deliverables which usually include the SBs, kits, and when requested, the embodiment, or – more usually – just the SBs and the kits.
The Technical Offer, which is a prerequisite for the Commercial Offer, advises on which items will be removed or installed, what is touched and what should be untouched, and which new items will be BFE versus SFE etc. It will also highlight which ATA Chapter expertise and competences will be required during the upgrade – eg. Ch 21 - Air Conditioning; Ch 24 - Electrical Power; Ch 25 – Equipment & Furnishings; Ch 38 – Water & Waste, and so on.
The Commercial Offer is also needed by the customer to engage with its chosen MRO to firm-up slots and work scope. For example, it enables them to understand when the first head-of-version will start the working party, the frequency and the cadence – eg one per month, or two per month etc..
Customer’s offer acceptance and project kick-off
Once the resulting final Technical & Commercial offer has been accepted by the customer, the official project kick-off meeting is convened during which Airbus assigns a dedicated Upgrade Programme Manager (UPM). The UPM will be there with the customer – from guidance with LOPA finalisation, providing access to Airbus’ expertise and resources in Cabin Engineering and DMU, taking them through the complete cabin certification process using the original Type Certificate (TC), updating the customer aircraft’s technical documentation, and even up until the last delivery of the kits and SBs to the customer, and as well the last working party. Even though the working party is not performed by Airbus, the UPM still remains the point of contact if the airline or MRO has any questions about the SB or or kit.
Accompanying the customer throughout the upgrade journey
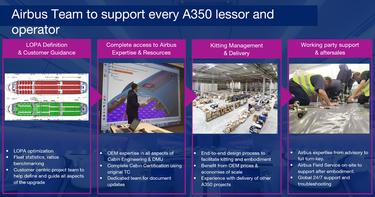
With the project fully underway, Airbus guides the customer every step through the journey from the beginning to its satisfactory completion. One person who will not change is the Airbus sales contact. There are other points of contact too. For example, once the customer requests the ROM offer, Airbus will assign to the customer a dedicated Offer Manager – who represents the team which has links with all the behind-the-scenes Engineering.
To further assist the embodiment to proceed smoothly and to plan, especially for the first of several aircraft entering the MRO working party on ‘D-day’, Airbus can provide its own experts (the actual engineers who had authored the SBs) on-site as advisors to the customer and their MRO. This approach ensures that there is nothing unclear on the drawings or SBs, and also serves as a ‘guiding hand’ with physical implementation of the first upgrade itself.
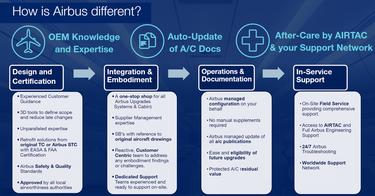
Your media contacts
Contact us
Martin Fendt
Airbus Corporate Communications - Airbus Commercial Aircraft
Sébastien Koeck
Upgrade Services Marketing Director
Marie-Charlotte Boissonneau
Airbus Upgrades Services Project Manager
Latest FAST articles
Continue Reading
Getting ready for A350 cabin retrofits
Web Story
FAST
The first A350s are reaching eight years in service, and the wave of cabin retrofits which is now starting will rapidly gain momentum over the next few yeaTurbulence alert - The collaborative network
Web Story
FAST
Intermittent repetitive failure
Web Story
FAST
End-of-life Reusing, recycling, rethinking
Web Story
FAST
In-flight health monitoring
Web Story
FAST