In-flight health monitoring
For on-time dispatch
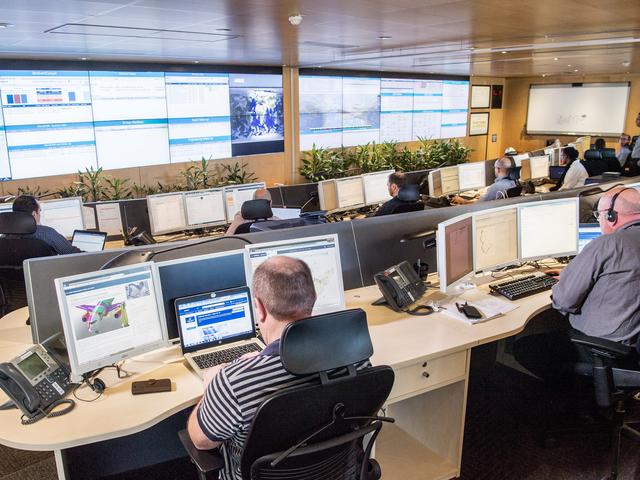
What if you could get a heads-up on the maintenance status of an aircraft before it even landed? You could be ready for any necessary work required and avoid - or at least minimise any potential delays.
In-flight events can generate unscheduled maintenance and have a huge impact on the availability of the fleet which can in turn generate costs. Managing these events efficiently and in real-time is one way to ensure efficient dispatch.
This is where health monitoring plays a key role.
Health monitoring - collecting and analysing data about issues or potential issues - has clearly evolved over the last thirty years, from time-consuming manual checks, to standalone pc-based software, to today’s fully web-based system.
Indeed, an increasing number of airlines consider it to be an essential part of their operations as they strive to become more and more proactive, to avoid AOGs and to dispatch their aircraft on time. And this is regardless of fleet size, with health monitoring adopted by airlines having only 2, or over 400 aircraft. Health monitoring is linked to usage not fleet size, with the key performance goal of avoiding delays and costly unscheduled maintenance.
Health monitoring: Real-time supervision of an aircraft's condition during flight, to prioritise the troubleshooting and plan maintenance related tasks.
Health monitoring for maintenance works by collecting technical data from door closure or engine start, then during flight and up to arrival at the gate. The overall gain for airlines is to dispatch the aircraft on time.
Monitoring in real time helps ground staff to make decisions and plan in advance, thus saving precious turnaround times. It gives the teams detailed information on potential issues or “events”. This in turn enables them to take appropriate decisions based on criticality, logistics and upcoming maintenance checks, and prepare in advance for repairs and replacements - all before the aircraft has even come in to land. Of course, all data collected could be used by the back-office team to handle less urgent issues and by the airline engineering teams for long-term analysis.
It is important to note that the maintenance fault and warning alerts referred to here can generally be considered as part of the normal operations of an aircraft. Indeed, the main purpose of health monitoring is to assist ground staff with decision-making to check and address common operational issues. It can also offer operators access to important parameters thanks to different reports.
A healthy evolution
From no health monitoring…
Imagine your aircraft flying to a destination where you don't have your own maintenance team to support you. Your maintenance staff are busy with other tasks, pending the arrival of the flight. Once the aircraft has landed and arrived at the gate, the team requests the local maintenance supplier (MRO) to connect to the aircraft’s system, retrieve and send the report. They may have to wait up to an hour, depending on the availability and responsiveness of the partner.
Once the data has been downloaded, the text report is transferred to the Maintenance Control Centre before the team peruses it. They start looking for information in the post-flight and ACMS reports. They need to correlate manually so, for example, if there is a fault and an associated warning, they need to analyse if it is about the same topic (unlike an online health monitoring system which can do this task automatically), then they need to find and use the right technical documentation (TSM, TFU).
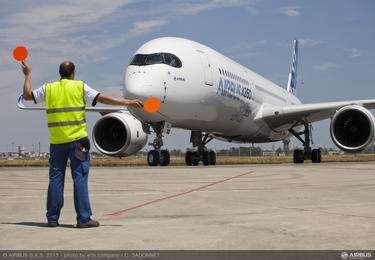
…to the first health monitoring system for Airbus operators
Over twenty years ago, many Airbus operators started using Airbus’s health monitoring software, Airman. This radically changed the management of maintenance for incoming aircraft.
Let’s look at the same flight using this solution.
From the moment the engines start warming up and/or the doors are closed, through to take-off, flight and landing, the maintenance teams are watching their monitors. They can see all alerts and warnings and Airman can correlate alerts and indicate if they are related.
If an alert is considered critical, the team has immediate access to all the details and technical documentation and can decide on the maintenance action. The team can exchange with their engineers and, based on the analysis, can decide to intervene as soon as the aircraft arrives. Before the aircraft lands, they can already launch the work order, organise part delivery, and prepare work procedures and manpower.
If an alert is considered non-critical, and for example the aircraft has a C-check planned the following week, they may decide to postpone the intervention until then or even later, depending on severity of the issue.
All-in-all, there is no waiting at the gate to download, check and correlate data. Decisions have all been made in advance of the landing and necessary interventions prepared.
…and now airlines get a power boost
Today, with ever evolving technology, health monitoring takes another step forward with a much more powerful platform, Airbus Skywise. But what additional benefits does this actually bring airlines?
Skywise Health Monitoring (SHM) takes advantage of all the benefits that information technology can now offer, thanks to a platform which is able to manage much bigger amounts of data, much faster. The teams can also associate the work order with the maintenance activities.
A fully web-based system - so with no need to have Java installed locally - means airlines can access the data regardless of their computer or tablet type.
By default SHM offers different information to ease troubleshooting. With each event the airline or its maintenance partner gets a short history of the last 15 flights. This enables it to identify repetitive events and to use solutions already applied before. On top of this, the flight phase specifies exactly when during the flight the event occurs, because an event may be critical during flight but not during engine start. The team can also go back much further in time to consult the PFR Post Flight Reports - for example, the last 100 reports.
The two features are used by the MCC, the real-time operators. They can access the full view of events over several years.
Defining priorities and severity of events
Monitoring failures or potential failures during flight has become standard practice and even indispensable. The actual severity of the event is evaluated by the qualified ground staff, with or without support from Airbus in line with the airline’s agreement / contract. It is the ground support people who make the decisions, not the aircraft system.
Airbus can provide some priorities linked to the fault. This assists the airline in evaluating the severity of the issue and consequently how to manage it.
Airlines may also choose to define their own priorities regarding maintenance. These may depend on their passenger offering, such as IFE, or their logistical set-up. Typically, an airline might prefer to fix a fault once the aircraft has returned to its main base, rather than during a stopover which could mean extra delays and costs. These priorities are programmed in the health monitoring system. In line with the support contract signed with the customer, health monitoring is also used by Airtac (the Airbus Technical AOG Centre) with a similar set-up to the customer, constantly monitoring the fleet 24/7.
Regulatory authorities may define parameters to be adhered to such as the Master Minimum Equipment List, requiring minimum equipment to be running before allowing dispatch. The health monitoring system can highlight if a no-go situation has been reached which requires a fault to be fixed first.
In addition to fault alerts, health monitoring also provides Aircraft Condition Monitoring System (ACMS) reports which include all key data of the aircraft and the parameter values. These reports serve to check that all parameters are working.
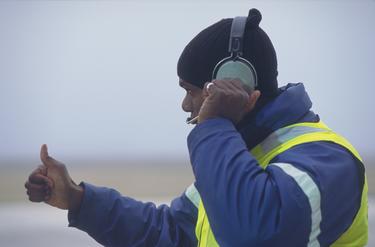
Health monitoring in 5 steps for the maintenance team
Step 1
At the beginning of the flight, there is a maintenance alert on the aircraft. We receive the alert by email because we have already set up notifications for a specific ATA chapter. We simply click on this event to connect to Skywise Health Monitoring enabling us to retrieve the whole context, ie the warnings and all the associated faults.
Thanks to the link made by SHM to the technical documentation, the system is able to aggregate several events in a fault case where we confirm that we have received a warning. However, this issue is not an isolated case: it is linked to other events in the flight and we have to consider the whole fault case in order to identify the appropriate action.
Step 2
In real time we are informed that this is a critical issue and, based on the Minimum Equipment List, we will not therefore be able to perform the next dispatch. So we anticipate a potential AOG, or maybe a less critical situation with dispatch under condition.
Step 3
To help prepare troubleshooting, the system has given us a full view of technical documentation related to our fault case. There are some specific observations to help select what to consult, and we now decide what to put in place to recover the situation.
Step 4
Health monitoring has also given us a view on all maintenance activities already performed or planned in the future and which may be linked to the current event. The alert may indeed be just a side effect of a past maintenance activity - or there may already be a future intervention planned which will fix the issue.
Step 5
We decide to launch a workflow related to this fault, taking into account maintenance constraints such as the availability of specific tools or skills.
In the system, we attach this work order to the fault case. All our colleagues in the airline are now informed that we have performed the troubleshooting, decided what to apply, and that this case is ongoing. This means that, between today and the day of execution of the work order, we will continue to operate the aircraft with everyone aware that the issue is managed, and there is no need to lose time doing it themselves. So in terms of operations, we are clearly more efficient.
Top new features in Skywise Health Monitoring (SHM)
- Supports tablets
- Generates workflows with improved task assignment and data-sharing functions
- Gives access to airline Maintenance Information data
- Integrates Customized Minimum Equipment List (MEL)
- Provides simple long-term analysis tool for Engineering
Confidentiality and Airbus intervention
This point is understandably absolutely crucial for airlines. An airline’s data is only visible to itself - and to a limited number of Airbus staff whose role is to support the Skywise application. Airlines can exchange information if they belong to the same company group. This enables them, if they so choose, to have just one dashboard covering all aircraft and to manage their maintenance at a group-wide level.
Airbus carries out regular audits on the Skywise platform to guarantee security of data for its customers. And a permanent team checks and ensures the compliance of access to the data entrusted to it.
When does Airbus intervene?
Airbus only ever intervenes to monitor the aircraft if the customer has agreed via a contract. This is the case for airlines using Flight Hour Services (FHS) - or Airtac if they require support with the Skywise platform.
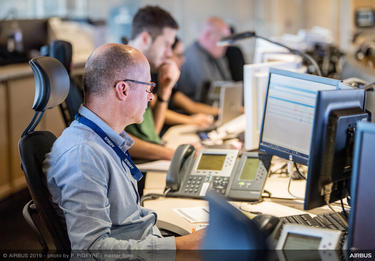
Health monitoring enables control centre, maintenance and engineering teams to anticipate troubleshooting, prepare for interventions and launch work as soon as the aircraft lands. It also provides direct links to the right documentation before proceeding to troubleshooting. It is also today the system used 24 hours a day by the Airbus Airtac team which manages the most critical breakdowns for some customers.
And as aircraft technology becomes more sophisticated, it is possible to gather even more data. This in turn means the capability to extract more powerful analytics whose purpose ultimately serves to assist both customers and Airbus in better understanding the aircraft, anticipating actions such as maintenance, and bringing real value to operations.
Photos and illustrations copyright Airbus. (Airbus: L. Borrel. Master Films: P. Pigeyre. exM: C. Sadonnet)
Latest FAST articles
Continue Reading
Getting ready for A350 cabin retrofits
Web Story
FAST
The first A350s are reaching eight years in service, and the wave of cabin retrofits which is now starting will rapidly gain momentum over the next few yeaTurbulence alert - The collaborative network
Web Story
FAST
Intermittent repetitive failure
Web Story
FAST
End-of-life Reusing, recycling, rethinking
Web Story
FAST
In-flight health monitoring
Web Story
FAST